Drewno klejone to wysokiej jakości produkt drzewny, mający szerokie zastosowanie. Charakteryzuje się doskonałymi parametrami wytrzymałościowymi, stabilnością wymiarów i nienaganną estetyką.
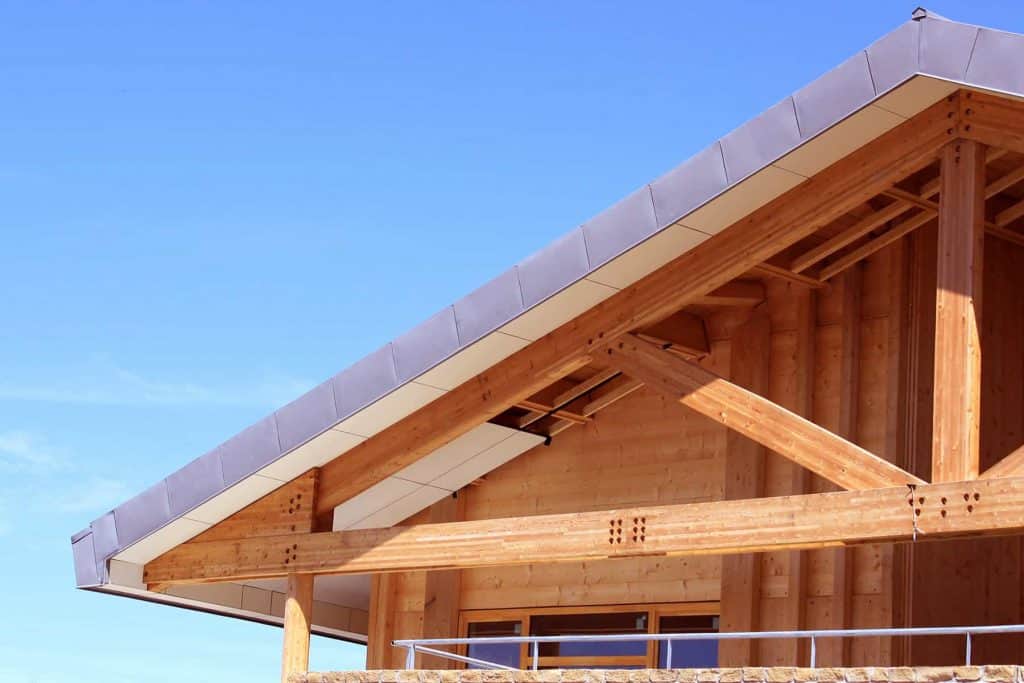
Drewno klejone
Klejonka stanowi dobrą alternatywę dla stali, żelbetu oraz innych materiałów konstrukcyjnych. W porównaniu z litym surowcem, drewno klejone warstwowo posiada wiele unikalnych zalet i właściwości. Występuje przy tym w kilku klasach, co pozwala na optymalne dopasowanie materiału do potrzeb inwestorskich.
Co to jest drewno klejone?
Drewno klejone to popularny materiał konstrukcyjny i powstaje na skutek sklejenia ze sobą krzyżowo wielu warstw drewnianych desek, zwanych lamelami. Posiada praktycznie wszystkie zalety swojego naturalnego surowca, a jednocześnie pozbawione jest wielu jego wad.
Podobnie jak tradycyjne lite drewno, cechuje się dużą wytrzymałością i stabilnością. Może dzięki temu służyć do budowy konstrukcji dachów i całych obiektów o oryginalnym kształcie oraz większej rozpiętości, sięgającej nawet 50 m.
Drewno klejone warstwowo nie ulega podkształceniem pod wpływem zmian wilgotności i temperatury. Materiał ten jest odporny i sztywny, dzięki czemu spełnia wymogi narzucone tradycyjnemu drewnu. Wynika to nie tylko z wykorzystania do produkcji odpowiednich partii surowca z kloca, ale również wieloetapowej obróbki.
Drewno klejone wymaga wcześniejszego wysuszenia oraz ostrugania. Procesy te pozbawiają materiał larw owadów, grzybów, pleśni oraz bakterii, a także innych czynników biologicznych o działaniu degradującym.
Klejone drewno wykorzystuje się przede wszystkim do wykonywania konstrukcji profilowanych, wielkowymiarowych lub narażonych na kontakt z wodą. Materiał ten może mieć też zastosowanie ozdobne, ze względu na estetyczny wygląd. Z drewna klejonego tworzy się konstrukcje o dowolnym kształcie.
Materiał ten coraz powszechniej wykorzystywany jest do produkcji elementów konstrukcyjnych. Wykonuje się z niego prefabrykowane dachy i ściany. Drewno klejone znajduje zastosowanie w produkcji drewnianych podłóg, płyt meblowych, schodów czy okien. Z drewna klejonego powstają także wiązary dachowe, więźby dachowe, konstrukcje dachów skośnych. Najczęściej są one w całości budowane z suszonych i ostruganych belek lub tarcicy impregnowanej. Konstrukcje te nie wypaczają się i są odporniejsze na wilgoć. Z drewna klejonego mogą być tworzone belki posiadające nietypowe kształty, np. łukowe.
Produkcją drewna klejonego zajmują się fabryki i warsztaty stolarskie. W tych drugich powstają przede wszystkim mniejsze elementy. Kilkanaście lameli łączy się klejem, a następnie unieruchamia ściskami.
W fabryce proces ten jest w pełni zautomatyzowany i odbywa się przy użyciu pras, co pozwala na wykonanie elementów wielkowymiarowych. Klejone drewno można też produkować na specjalne zamówienie, zgodnie ze wskazaniami projektanta danej konstrukcji.
Producenci drewna klejonego zaczynają proces produkcji od suszenia komorowego lameli do wilgotności 8-12 proc. Następnie są one strugane oraz sortowane maszynowo lub ręcznie, po czym trafiają do odgórnie ustalonych klas wytrzymałości. Na tym etapie usuwane są wszelkie niedoskonałości drewna, np. oflisy czy większe sęki. Następuje ich automatyczne zaznaczenie oraz wycięcie.
Lamele o różnej długości posiadają końcówki, na których frezowane są zazębiające się ze sobą złącza klinowe. Ulegają one ściśnięciu oraz sklejeniu. Lamele należy przyciąć na pożądaną długość. Na szersze powierzchnie nanoszony jest klej. Kleje układane są warstwami, po czym ulegają sprasowaniu. Po wyschnięciu kleju belki można ostrugać, a krawędzie poddać frezowaniu. Wycięcie niedoskonałości drewna oraz przeprowadzenie klejenia warstwowego lameli pozwala na uzyskanie produktu o doskonalszych parametrach.
Pod względem estetycznym drewno klejone nie ustępuje litemu. Kleje używane do łączenia lameli są odporne na wodę, a przy tym odpowiednio dobierane kolorystycznie. Połączenia elementów nie rzucają się dzięki temu w oczy. W zależności od potrzeb, wybrać można drewno z sękami lub też materiał niemal całkowicie ich pozbawiony.
Elementy konstrukcyjne wbudowane wewnątrz budynku nie wymagają żadnych dodatkowych zabezpieczeń. Jeżeli natomiast po zastosowaniu pozostają widoczne, można pokryć je przezroczystą lub kryjącą powłoką dekoracyjną.
W przypadku drewna klejonego stosowanego na zewnątrz, warto ochronić je impregnatem przed wilgocią, grzybami i glonami. Innym rozwiązaniem jest zastosowanie powłoki dekoracyjnej, np. z oleju lub lakieru.
Zazwyczaj krawędzie elementów konstrukcyjnych wykonanych z drewna klejonego są zaoblone. Rozwiązanie to zwiększa odporność na ogień. Płomień nie jest w stanie przedostać się w głąb elementu, ponieważ porusza się wyłącznie po powierzchni. Drewniane elementy konstrukcyjne z drewna klejonego poddawane są impregnacji.
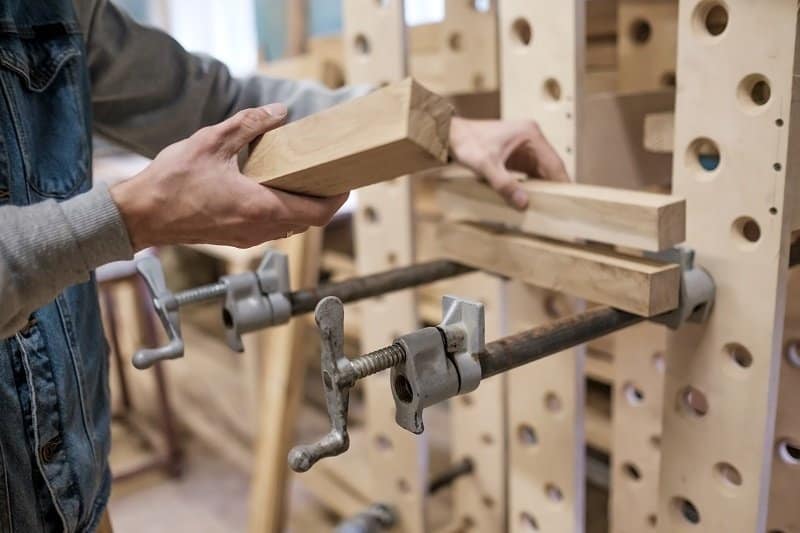
Drewno klejone
Z jakich gatunków drewna robi się klejonkę i jak wygląda proces produkcji?
Szczególnym rodzajem drewna klejonego jest klejonka. To typ płyty meblowej, krawędziarki lub kantówki o określonym przekroju.
Powstaje z drewna klejonego warstwowo oraz znajduje szerokie zastosowanie w stolarce i budownictwie. Klejonkę najczęściej produkuje się z litego drewna odmian iglastych lub liściastych. Gotowy wyrób jest bardziej wytrzymały, a przy tym tańszy niż ten z klejonki litej. Dzięki mnogości połączeń klejowych, taki produkt posiada bardzo dużą odporność. Klejonkę klasyfikować można na różne sposoby. Najbardziej powszechny jest podział ze względu na metodę wykonania.
Tradycyjne metody produkcji klejonki praktykowane są przez zakłady rzemieślnicze. Polegają one na sklejaniu ze sobą elementów tarcicy przy użyciu ścisków.
Poza tradycyjną klejonką jednowarstwową, producenci często wytwarzają także inne jej typy. Do najpopularniejszych należą płyty sztorcowe, trójwarstwowe oraz twardzielowe. W przypadku płyt trójwarstwowych, lamele poszczególnych warstw ułożone są do siebie prostopadle. Taki wyrób cechuje się podwyższoną odpornością na zmiany wilgotności, przez co jest trwalszy od zwykłych płyt.
Klejonka powstaje z tarcicy, jednak jest wobec niej wyrobem komplementarnym. To produkt całkowicie naturalny, a tym samym ekologiczny. Charakteryzuje się dużymi walorami estetycznymi oraz użytkowymi.
Klejonkowe blaty są mniej podatne na wyginanie, paczenie i pękanie. Wykonane z klejonki schody zachowują swój kształt nawet po wielu latach eksploatacji i nie trzeszczą pod stopami. Klejonkę stosuje się głównie w wewnątrz domów. Standardowo do klejenia wykorzystuje się preparaty zapewniającymi odpowiednią odporność spoiny klejowej. Dzięki temu powierzchnia może być bez przeszkód użytkowana oraz myta.
Klejonka znajduje zastosowanie w meblarstwie. Powstają z niej nogi stołów i krzeseł, a także słupy do stolików klejone warstwowo na grubość. Kilka warstw desek należy na początek skleić, a następnie przyciąć, ostrugać lub oszlifować. W ten sposób uzyskiwane są pożądane gabaryty. Materiał można też pokryć laminatem lub okleinami, aby uzyskać ozdobny profil.
Klejonka może być wyprodukowana z praktycznie dowolnych gatunków drewien. W Polsce najczęściej wykorzystuje się w tym celu świerk, a także sosnę oraz różne odmiany liściaste – jesion, klon i dąb. Zdecydowanie najczęściej klejonka powstaje jednak z drewna świerkowego. Charakteryzuje się ono dobrymi parametrami wytrzymałościowymi. Posiada przy tym efektowny i atrakcyjny wygląd. Świerkowy surowiec wykazuje ponadto dużą odporność na wilgoć. W przypadku zmian wilgotności powietrza zachowuje optymalną stabilność. Drewno to nie jest jednak podatne na impregnację. Jeżeli zatem konstrukcja wymaga dodatkowego zabezpieczenia, lepszym rozwiązaniem będzie drewno sosnowe. Proces impregnacji pod ciśnieniem nieco wydłuża proces produkcji.
Zaimpregnowane deski muszą schnąć aż do momentu wyrównania wilgotności w każdym przekroju. Jeżeli natomiast klejonka będzie regularnie narażona na działanie opadów atmosferycznych, najlepszym rozwiązaniem jest drewno modrzewiowe. Nie bez znaczenia pozostaje jednak dostępność rynkowa. Pod tym względem zdecydowanie przoduje drewno świerkowe. W przypadku jodły, modrzewia czy sosny, należy więc mieć na uwadze wysokie prawdopodobieństwo oczekiwania na gotową klejonkę.
W zależności od docelowego zastosowania, lamele przeznaczone do klejenia wyciąć można z różnych części kloca. W przypadku konstrukcji mających znosić największe obciążenia, wykorzystuje się lamele wykonane wzdłużnie z twardzieli – najtwardszej części bali. Elementy mniej wymagające powstawać mogą z lameli o praktycznie dowolnych parametrach. Drewno przeznaczone do klejenia da się wycinać także w poprzek słojów, czyli sztorcowo.
Najczęściej do produkcji klejonki stosuje się klej melaminowy. Nieco rzadziej wykorzystywany jest także klej rezorcynowy. Masa klejowa połączona z drewnem zyskuje po utwardzeniu równomierne parametry. Posiada taką samą odporność na wilgoć, gnicie czy ogień. Stosowane kleje są w pełni bezpieczne, nawet w przypadku kontaktu z ogniem. Nie emitują też żadnych szkodliwych substancji. W zależności od wykorzystanego kleju, inny może być kolor fugi. Wyroby z klejem melaminowym posiadają barwę szarą, a te z klejem rezorcynowym odcień zbliżony do ciemnobrązowego.
Produkcja klejonki rozpoczyna się od odpowiedniego przygotowania drewna. Należy przetworzyć je na bloki o identycznych wymiarach, czyli tarcicę. Następnie jest ona suszona w specjalnych suszarniach, celem uzyskania dopuszczalnej wilgotności drewna 2-12 proc.
Kolejny etap do usunięcie niedopuszczalnych wad oraz przebadanie surowca pod względem wytrzymałości. Następnie konieczne jest przeprowadzenie obróbki mechanicznej. Na tym etapie odbywa się frezowanie czoła desek, dzięki któremu uzyskać można tzw. złącza palczaste. Na nie nakładany jest klej, co pozwala na połączenie desek w długie listwy. W takiej postaci należy pozostawić je do wyschnięcia kleju.
Kolejny krok wymaga ostrugania listew na taką samą grubość. Na ich bloki nakładany jest klej, po czym elementy ustawia się na prasie oraz ściska do czasu wyschnięcia łączeń. Uzyskana w ten sposób klejonka może być poddana dalszej obróbce. Na etapie produkcji duże znaczenie ma kontrola wilgoci tarcicy, jakości szlifowania desek, wytrzymałości złącz palczastych, stopnia nacisku pod prasą oraz parametrów kleju.
Przygotowane deski łączone są we wstęgi. Wyfrezowane czoła desek tworzą złącza palczaste, pokrywane następnie klejem. Deski tworzą długie listwy po ściśnięciu. Lamele odstawiane są w złączach do całkowitego wyschnięcia, po czym poddawane są struganiu do wymaganej grubości. Grubość zależy od pożądanych właściwości elementu oraz jego konkretnych zastosowań.
Nieduże promienie gięcia można uzyskać w przypadku bardzo cienkich lameli, które da się swobodnie wyginać. W gotowej klejonce zawartość kleju jest zaskakująco niska i wynosi mniej, niż 1 proc. Drewno układa się następnie w specjalnej prasie, umożliwiającej nagięcie jej do wymaganego kształtu.
Na etapie schnięcia, ściśnięte deski powinny przebywać w temperaturze minimum 40 stopni Celsjusza. W ten sposób uzyskać można wytrzymałe, odporne i trwałe złącze. Aby ochronić materiał przed nadmiernym przesuszeniem, warto zadbać o prawidłową wilgotność powietrza.
Po utwardzeniu się kleju klejonka jest gotowa i posiada pożądany kształt. Materiał należy poddać obróbce końcowej, polegającej na mechanicznym docięciu końcówek elementów. W razie potrzeby można też wykonać wymagane wcięcia i otwory, nałożyć okucia czy dokonać konserwacji powierzchni. Po zakończeniu prac, drewno klejone pakowane jest w folię oraz transportowane w wybrane miejsce.
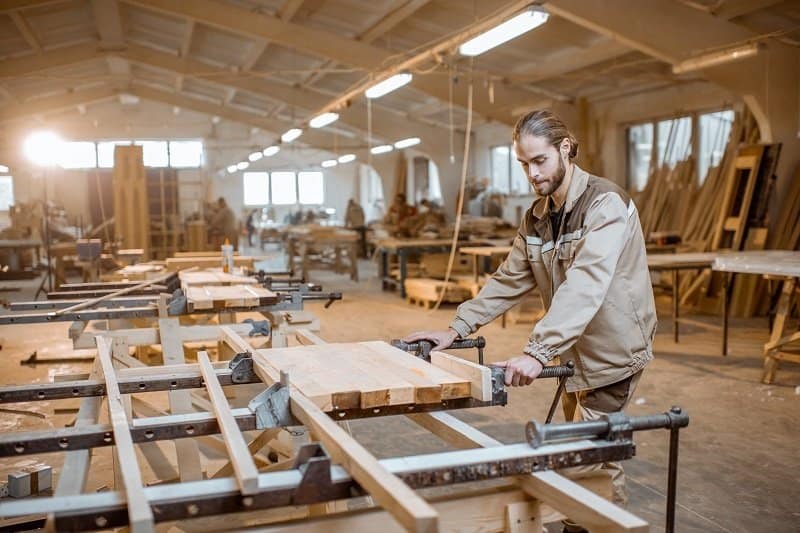
Drewno klejone czy lite
Drewno klejone czy lite? Porównanie parametrów
Lite drewno jest surowcem od bardzo dawna znanym ludzkości. Służy jako opał i kompozyt, znajduje zastosowanie w budownictwie i sprawdza się przy produkcji mebli. Należy do najpopularniejszych materiałów konstrukcyjnych zarówno więźb dachowych, jak i całych budynków.
Drewno lite coraz częściej zastępowane jest klejonym, będącym wynalazkiem dużo młodszym. W porównaniu z tradycyjnym surowcem, wykazuje większą odporność na działanie czynników zewnętrznych. Posiada też lepsze właściwości mechaniczne. Drewno lite cechuje się większą podatnością na uszkodzenia, zagrożenia biologiczne i deformacje.
Przewaga drewna klejonego wynika w dużym stopniu z samego procesu produkcji. Staranne suszenie komorowe, struganie, sortowanie na zdefiniowane klasy wytrzymałości znacząco sprzyja utworzeniu solidnego i trwałego materiału. Pozwala na usunięcie największych wad surowca, takich jak duże sęki. Wszystkie niedostatki są automatycznie zaznaczane oraz wycinane.
W przypadku wzdłużnego połączenia lameli z drewna litego na mikrowczepy, powstaje konstrukcyjne drewno lite KVH. W ten sposób połączone krótkie fragmenty drewna umożliwiają budowę konstrukcji o niemałej wytrzymałości.
Mikrowczepy to stożkowe, nieduże nacięcia na końcach drewna. Wykonuje się je w taki sposób, aby wystające z pierwszego elementu stożki mogły wypełniać zagłębienia w drugim fragmencie drewna. Jeżeli natomiast wąskie paski drewna zostaną sklejone warstwowo, powstaje drewno konstrukcyjne BSH. Pozwala ono na budowę elementów konstrukcyjnych o bardzo dużych rozpiętościach.
Klejone drewno da się wyginać. Można też łączyć lamele w taki sposób, aby uzyskać elementy o praktycznie dowolnym kształcie. Elementy z drewna klejonego KVH mogą mieć długość maksymalnie kilkunastu metrów. Z drewna klejonego BSH powstają natomiast wyroby o długości nawet kilkudziesięciu metrów. Zdaniem niektórych producentów drewna klejonego, limit zależy tak naprawdę od możliwości transportu.
W porównaniu z drewnem litym, drewno klejone charakteryzuje się większą stabilnością kształtu. W stanie zmontowanym, to pierwsze znacznie szybciej wysycha i wykrzywia się. W niesprzyjających warunkach mogą też pojawić się pęknięcia.
Powodem braku szczelności ścian zewnętrznych oraz szkód związanych z obecnością wilgoci jest zwykle zbyt mokre drewno w czasie montażu. Dla bali i desek z drewna litego charakterystyczna jest ich podatność na nieustanne kurczenie się oraz pęcznienie, co stanowi reakcję na zmianę warunków atmosferycznych.
Drewno klejone warstwowo ma bardziej zrównoważoną wilgotność, optymalnie dopasowaną w stanie wybudowanym. Dzięki obróbce nie paczy się i posiada znikomą tendencję do pękania. Sprawdza się bardzo dobrze do tworzenia elementów budowlanych, które mają stanowić podstawę szczelnych i stabilnych konstrukcji, na przykład dźwigarów klejonych. Pozwala na wznoszenie systemów nośnych o rozległej rozpiętości. Nie wymagają one podpór, nawet mimo wykorzystania wąskich elementów. Przy stosunkowo niskiej masie własnej, drewno klejone ma też zaskakująco wysoką zdolność nośną.
Konstrukcja wykonana z drewna klejonego jest lekka i estetyczna. Elementy połączone z innymi materiałami pozwalają na zniwelowanie mostków cieplnych. W porównaniu do litego, takie drewno nie wymaga też dodatkowej impregnacji biologicznej. Grzyby wymagają do rozwoju wilgoci, którą w przypadku klejenia warstwowego da się wyeliminować. Z chemicznych środków ochronnych zrezygnować można w zdecydowanej większości przypadków.
Klejone drewno wyróżnia się ponadto sporą ogniotrwałością, co pozostaje nie bez znaczenia w przypadku elementów nośnych budynku. Podpory wykonane z klejonego drewna nie skręcają się, co chroni łuki przed utratą stabilności. Nie przypadkiem materiał ten sprawdza się przy budowie pasaży handlowych, hal sportowych, basenów czy dużych sal wystawienniczych.
Lite bale mają ograniczoną długość, a tym samym uniemożliwiają opłacalną realizację takich projektów. Drewno klejone pozwala na uzyskanie praktycznie dowolnych kształtów. Mając na uwadze koszty całkowite budowy, konstrukcje z klejonego drewna są zdecydowanie bardziej ekonomiczne. Korzystnie wypadają nawet w porównaniu z betonem i stalą. Są lżejsze, co ogranicza konieczność stosowanie dźwigarów klejonych o dużej wysokości oraz przekrojów konstrukcji podtrzymujących. W konsekwencji koszty transportu i budowy są znacznie niższe.
Drewno klejone cechuje się wyższą ognioodpornością. Kantówki posiadają gładko ostruganą powierzchnię, dzięki czemu płomienie się po niej prześlizgują i zapłon jest utrudniony. Jeżeli jednak dojdzie po pewnym czasie do zajęcie się elementu, zwęgli się jedynie warstwa zewnętrzna. Może ona przez dość długi czas izolować przed ogniem warstwy wewnętrzne.
Lite drewno w stosunkowo niedługim czasie może zacząć pękać. Szczeliny powstałe w belkach przyciągają mikroorganizmy i zanieczyszczenia. Nie pomaga nawet impregnacja powierzchni środkami grzybobójczymi. Lite bale mogą się także wykrzywiać i skręcać, co stanowi zagrożenie dla użytkowników.
Nie oznacza to jednak, że tradycyjny surowiec nie posiada żadnych atutów. Wiele zależy od jego jakości. Spore zapotrzebowanie na ten materiał sprawia, że często nie jest ono wystarczająco dokładnie wysuszone. Proces ten powinien odbywać się w zakresie 1 roku na 1 cm grubości drewna.
Dowodem na długowieczność prawidłowo wysuszonego drewna są konstrukcje i budynki historyczne, w całości wykonane z litego materiału. Warto pamiętać, że drewno klejone wciąż pozostaje drewnem. To naturalny materiał, na którym mogą pojawić się niewielkie rysy i pęknięcia. Nie wpływają one jednak na ogólną stabilność oraz trwałość wyrobów – właśnie dzięki temu, że zostały sklejone z kilku warstw.
Impregnacja i konserwacja drewna klejonego
Klejonka do zastosowań wewnętrznych spełnia rygorystyczne normy wilgotności, w związku z czym praktycznie nie potrzebuje dodatkowych zabiegów impregnacyjnych. Suszenie w odpowiednich warunkach w zupełności chroni materiał przed negatywnym działaniem czynników biologicznych.
W zachodnioeuropejskich krajach zwykle unika się stosowania dodatkowych zabezpieczeń dla tego materiału. W perspektywie długoterminowej, środki owadobójcze mogą bowiem negatywnie wpływać na ludzkie zdrowie. Polskie normy narzucają jednak konieczność przeprowadzania powierzchniowej impregnacji biologicznej.
W przypadku drewna klejonego o zastosowaniach zewnętrznych wygląda to nieco inaczej. Taki materiał jest zdecydowanie bardziej narażony na działanie czynników atmosferycznych, co wymusza zastosowanie dodatkowych środków ochrony.
Podobnie jak inne materiały konstrukcyjne, drewno klejone wymaga przeprowadzania określonych zabiegów zabezpieczających. W większości ich wykonanie nie jest skomplikowane. Znacząco jednak przyczynia się do przedłużenia żywotności wyrobów z klejonego drewna oraz zachowania ich jakości.
Podstawowym zabiegiem zabezpieczającym jest impregnacja, czyli zastosowanie specjalnych środków ochronnych. Drewno klejone standardowo poddawane jest impregnacji ciśnieniowej. Robiąc to samodzielnie, należy pamiętać o przestrzeganiu zasad podanych przez producenta wybranego preparatu. Drewna niezabezpieczonego nie powinno się pozostawiać na działanie warunków atmosferycznych. W razie takiej konieczności, zastosować można dodatkową ochronę fizyczną – np. plandekę lub zadaszenie.
Elementy drewniane często docierają do inwestorów w dokładnie zapakowanych foliach. Nierzadko są one umocowane bardzo ciasno. Taki towar należy rozpakować w możliwie najszybszym czasie. Umożliwi to prawidłową wentylację klejonego drewna i ochroni je przed przedwczesnym zniszczeniem. Jeżeli materiał został uprzednio zabezpieczony impregnatem, ochrona powinna być długotrwała. Drewno jest jednak surowcem naturalnym, który potrzebuje powietrza.
Swoistym zabezpieczeniem jest także możliwość przemalowania materiału na dowolny kolor. Opcja ta podnosi głównie walory estetyczne wyrobu, ponieważ sama impregnacja nie zabezpiecza barwy. W perspektywie paroletniej, niepomalowane drewno prawdopodobnie zmieni swój pierwotny kolor na bardziej zielonkawy.
Pozostałe zabiegi nie odbiegają znacząco od tych dokonywanych w przypadku drewna zwykłego. Klejone drewno narażone jest na działanie niekorzystnych czynników atmosferycznych, takich jak deszcz, śnieg, grad czy nadmiar słońca. Z uwagi na sporą wytrzymałość i dużą twardość, zabezpieczanie przed uszkodzeniami mechanicznymi nie jest konieczne.
Drewno klejone warto natomiast zaimpregnować celem ochrony biologicznej. Preparat można też nakładać pędzlem. Najlepsze efekty przynosi jednak impregnacja w specjalnej komorze ciśnieniowej lub zastosowanie metody zanurzeniowej.
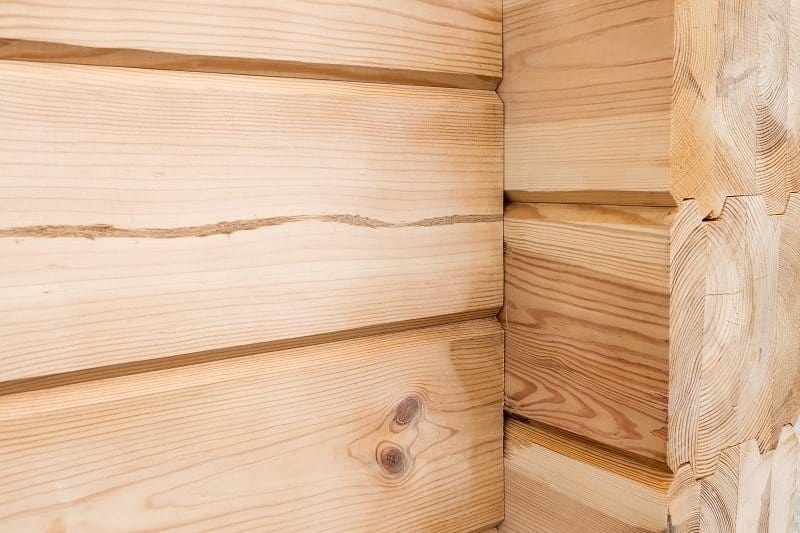
Zalety drewna klejonego
Zalety drewna klejonego
- Drewno klejone pozwala na wykonanie wyrobów o dużej wytrzymałości i sztywności. Materiał ten nie jest podatny na skręcanie, paczenie oraz pękanie.
- Prawidłowo wysuszone i zabezpieczone drewno klejone odporne jest także na wilgoć, wysokie temperatury oraz środki chemiczne.
- Można z niego budować konstrukcje o dużej rozpiętości.
- Pozwala na swobodne formowanie w wygięte łukowo kształty.
- Konstrukcja z drewna klejonego jest przy tym bardzo lekka, jednak zachowuje wytrzymałość zbliżoną do stalowej.
- Z reguły elementy z drewna klejonego montowane są za pomocą klasycznych dźwigów. Ciężar materiału jest nieduży, dzięki czemu można zaoszczędzić na transporcie wyrobów oraz wynajmie ciężkich maszyn.
- Duża trwałość drewna klejowego wynika zarówno z cech naturalnego surowca, jak i faktu zastosowania odpowiednich mas klejowych. Przekłada się to na zwiększoną odporność na warunki atmosferyczne oraz wodę. Nawet przy braku dodatkowej impregnacji, klejone drewno może być użyte na basenie czy w obiekcie sportowym.
- Wykonane z klejonki belki zapewniają dużą stabilność pod obciążeniem ogniowym.
- Nie bez znaczenia pozostaje wyjątkowo niski współczynnik przewodzenia ciepła. Materiał ten stosować można zarówno w wysokich, jak i niskich temperaturach. Komfort cieplny pomieszczeń zawsze pozostaje optymalny.
- Poszczególne elementy klejonki można bez trudu wytworzyć i połączyć na placu budowy. Przekłada się to na szerokie wykorzystanie drewna klejonego w produkcji wiązarów dachowych oraz innych konstrukcji prefabrykowanych. Jeżeli zachodzi taka konieczność, elementy można poddać obróbce przy użyciu ręcznych narzędzi.
- Rozwój technologii pozwolił na znaczne udoskonalenie drewna klejonego. Obecnie jest on produktem bardzo zaawansowanym. Jego produkcja została w dużym stopniu uprzemysłowiona, co doprowadziło do maksymalnej optymalizacji tego procesu.
- Dużym atutem drewna klejonego jest jego elastyczność. Aby utworzyć do wszelkiego rodzaju elementy nośne czy łuki, wystarczy wygiąć na etapie produkcji cienkie lamele w pożądany kształt.
- Montaż elementów z drewna klejonego da się przeprowadzić niezależnie od pogody, nawet w okresie zimowym.
- Zaletą drewna klejonego pozostają jego walory estetyczne. Materiał ten wprowadza do pomieszczeń przystępny klimat, który sprzyja relaksacji oraz pracy umysłowej. Wykończone klejonką wnętrza są komfortowe, przytulne i ciepłe.
- Drewno klejone warstwowo wykorzystać można nawet jako jedyny materiał konstrukcyjny. Da się też łączyć jego elementy z żelbetem lub innymi technologiami.
- Odpowiednio przygotowując surowiec w czasie produkcji, można kształtować go praktycznie dowolnie. Pozwala to na uzyskanie łuków, owali oraz innych problematycznych form.
- Drewno klejone powstaje z desek, które posiadają określone parametry wytrzymałościowe i wilgotnościowe. Zostały one odpowiednio ujednolicone. Wszelkie materiały stosowane do produkcji klejonego drewna podlegają ścisłym kontrolom jakościowym. Producenci drewna klejonego mogą dzięki temu osiągać parametry nieosiągalne dla drewien litych. Mimo tych właściwości, drewno klejone posiada stosunkowo niewielki ciężar. Nadaje się idealnie do budowy obiektów o jednoprzestrzennych, rozległych powierzchniach. Sprawdzają się np. w przypadku budynków użyteczności publicznej czy magazynów przemysłowych. Ze względu na brak konieczności stosowania podpór, wnętrza tych obiektów są bardzo funkcjonalne.
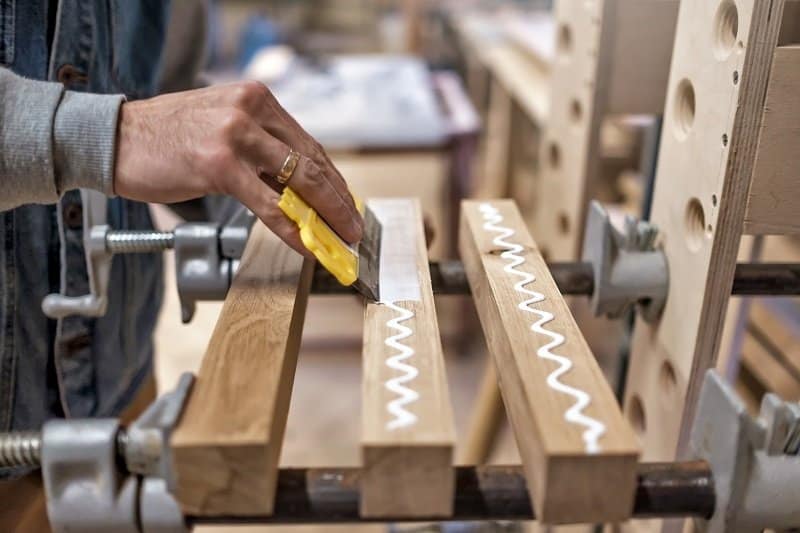
Wady drewna klejonego
Wady drewna klejonego
- Główną wadą tego materiału jest jego wysoka cena. Koszt inwestycji może nawet być nawet czterokrotnie wyższy, niż w przypadku zastosowania tradycyjnego drewna.
- Problematyczna jest również stosunkowo niewielka liczba producentów, którzy zajmują się produkcją klejonki. Nierzadko wiąże się to z koniecznością transportu elementów na duże odległości. W konsekwencji dodatkowo wzrastają koszty inwestycji, a także przedłuża się czas oczekiwania na produkt.
- W zależności od rodzaju konstrukcji, sam montaż może wymagać zastosowania dużych dźwigów oraz innego ciężkiego sprzętu.
Klasy i parametry drewna klejonego
W ciągu ostatnich kilkunastu lat wprowadzono wiele zmian w normach dotyczących klejonego drewna. Projektanci, wykonawcy oraz inwestorzy muszą przede wszystkim zwracać uwagę na nazewnictwo poszczególnych klas oraz ujednolicenie przepisów w krajach europejskich. Drewno klejone opisuje się symbolem GL oraz oznaczeniem cyfrowym, czasem z dodanymi małymi literami.
Do 2015 roku wyróżniano cztery główne klasy drewna klejonego :
- GL24,
- GL28,
- GL32,
- GL36.
Obecnie jest ich siedem i zaliczają się do nich:
- GL20,
- GL22,
- GL24,
- GL26,
- GL28,
- GL30,
- GL32.
Różnice miedzy poszczególnymi klasami są aktualnie bardziej subtelne, niż przed zmianą.
Z normy usunięto też najwyższą klasę, czyli GL36. Jest to spowodowane praktycznym brakiem dostępności drewna posiadającego tak wyśrubowane parametry. Obecnie nawet klasa GL32 jest trudno dostępna.
W sprzedaży najłatwiej dostać można klasy GL24h, GL28c i GL30c. Trudniej dostępne to przede wszystkim GL28h i GL30h. Praktycznie nie do zdobycia są klasy GL32c oraz GL32h, których stosowania w projektach domów z reguły się unika.
Litery GL oznaczają odporność materiału na zginanie, określaną w N/mm2. Im numer ten jest wyższy, tym lepsza wartość tego parametru.
W przypadku oznaczenia zakończonego literą c, lamele zewnętrzne utworzone są z drewna o wysokich parametrach wytrzymałościowych, a lamele wewnętrzne posiadają mniejszą wytrzymałość. Oznaczenie „c” to „combined”, czyli wariant mieszany.
Jeżeli natomiast drewno klejone oznaczone jest literą „h”, dużą wytrzymałością cechują się elementy zarówno wewnętrzne, jak i zewnętrzne. Oznaczenie „h” to „homogeneous”, czyli wariant jednorodny.
W przypadku braku oznaczeń, drewno prawdopodobnie jest niskiej jakości i posiada słabe lamele wewnętrzne.
Poza oceną jakości konstrukcyjnej, klasy drewna klejonego służą także ocenie jakości wizualnej. Nsi to standardowa, przemysłowa klasa wizualna. Opisane nią wyroby stosowane są tam, gdzie większe znaczenie mają parametry konstrukcyjne niż estetyczne. W drewnie klejonym Nsi dopuszcza się występowanie różnych mankamentów wizualnych, np. śladów po owadach, zabrudzeń, przebarwień czy pozostałości żywicy. Akceptowalne są także luźne, wypadające i mocno zrośnięte sęki.
Drewno klejone klasy Si posiada wyższe walory dekoracyjne. W tym przypadku dopuszcza się nieduże dziury po owadach i mocno zrośnięte sęki. Większe uszkodzenia w drewnie klasy Si poddawane są szpachlowaniu.
Wszystkie z wyodrębnionych klas klejonego drewna posiadają określone parametry. Dotyczy to przede wszystkim kwestii związanej z wytrzymałością na:
- zginanie,
- rozciąganie oraz ściskanie wzdłuż i w poprzek włókien,
- ścinanie.
Znaczenie ma także średni moduł sprężystości i 5% kwantyl modułu sprężystości wzdłuż i w poprzek włókien.
Określa się równie takie parametry, jak średnia gęstość oraz gęstość charakterystyczna. Projektowanie wielkowymiarowych elementów wydaje się mieć sens w wyższych klasach, np. GL28c czy GL30c.
W przypadku elewacji, tarasów, wiat, altan, więźb oraz innych mniejszych projektów, rozsądniejszym rozwiązaniem jest klasa GL24h. Drewno o takich parametrach dostępne jest bardzo łatwo, co znacząco usprawnia zakup i procesy logistyczne. Nie bez znaczenia pozostaje atrakcyjna cena, nawet w sezonie.
Niektóre parametry wytrzymałościowe w klasie „c” są stosunkowo niskie w porównaniu do klasy „h”. Wytrzymałość na ściskanie czy zginanie jest jednak w obu przypadkach taka sama, a sprężystość różni się nieznacznie. Optymalizacja zużycia tarcicy sprawiła, że w przypadku wysokich klas łatwiej i taniej jest dostać produkty z oznaczeniem „c”.
Drewno klejone cena
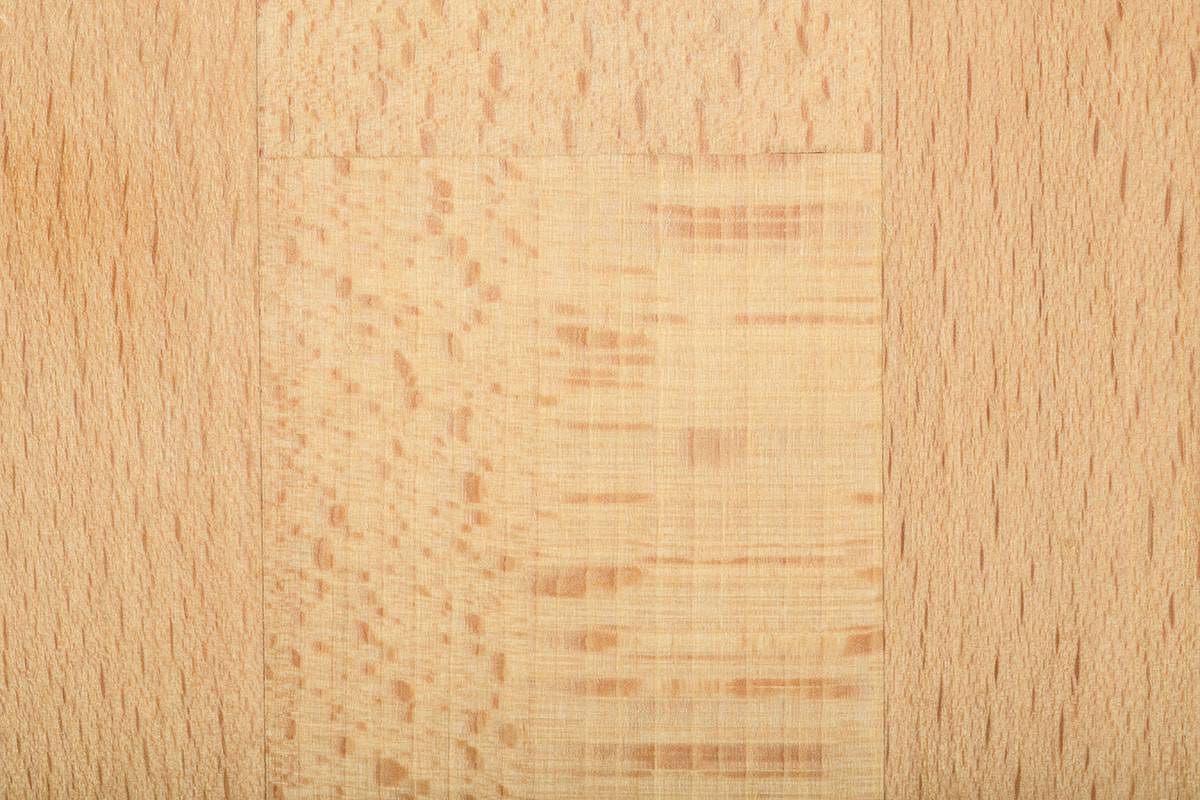
Drewno klejone cena
Cena drewna klejonego jest wysoka, w związku z czym wykorzystuje się ten materiał przy dużych rozpiętościach i mocno obciążonej konstrukcji.
FAQ
Ile kosztuje drewno klejone?
Cena drewna klejonego jest wysoka, w związku z czym wykorzystuje się ten materiał przy dużych rozpiętościach i mocno obciążonej konstrukcji. Przykładowo ceny drewna klejonego za mb brutto: BSH Si 200x200 mm - 138zł, BSH Si 100x100 mm - 35zł, BSH Si 60x120 mm - 25zł.
Jakie są wady drewna klejonego?
Najczęściej wymieniane wady drewna klejonego to wysoka cena, niewielka liczba producentów oraz konieczność użycia specjalistycznego sprzętu przy montażu elementów o dużej rozpiętości.
Jakie są parametry drewna klejonego warstwowo?
Parametry drewna klejonego GL24h to: wytrzymałość na zginanie: 24 N/mm2, wytrzymałość na rozciąganie wzdłuż włókien: 19,2 N/mm2, wytrzymałość na rozciąganie w poprzek włókien: 0,5 N/mm2, wytrzymałość na ściskanie wzdłuż włókien: 24 N/mm2, wytrzymałość na ściskanie w poprzek włókien: 2,5 N/mm2, wytrzymałość na ścinanie: 3,5 N/mm2, średni moduł sprężystości wzdłuż włókien: 11 500 N/mm2, 5% kwantyl modułu sprężystości wzdłuż włókien: 9 600 N/mm2, średni moduł sprężystości w poprzek włókien: 300 N/mm2, 5% kwantyl modułu sprężystości w poprzek włókien: 250 N/mm2, gęstość charakterystyczna: 385 kg/m3, średnia gęstość: 420 kg/m3.