Drewno konstrukcyjne to surowiec o bogatej tradycji. Dzięki doskonałym parametrom wytrzymałościowym oraz powszechnie stosowanym, nowoczesnym metodom obróbki, stanowi ono doskonałą alternatywę dla betonu, stali i innych materiałów budowlanych.
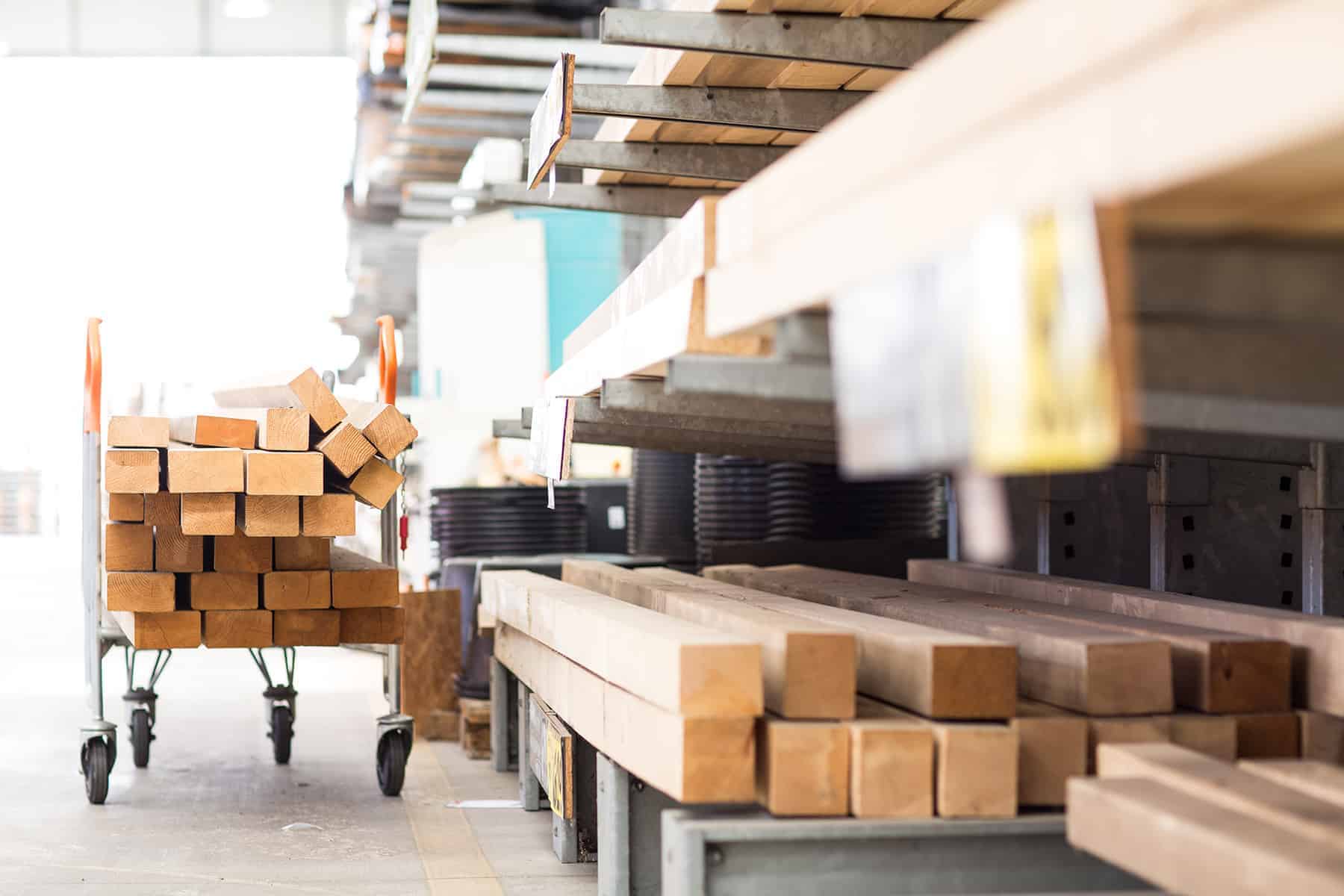
Drewno konstrukcyjne
Co to jest drewno konstrukcyjne?
Drewno konstrukcyjne to niezwykle wszechstronny, wytrzymały materiał o ściśle określonych parametrach, wykorzystywany powszechnie do wznoszenia stabilnych konstrukcji budowlanych oraz dachowych. Do konstrukcji różnego rodzaju obiektów budowlanych wykorzystuje się zarówno odpowiednio przygotowane drewno lite, jak i drewno klejone o podwyższonej wytrzymałości.
Najwyższej jakości drewno konstrukcyjne sprowadzane jest zwykle do Polski z zagranicy, przede wszystkim ze Skandynawii. Skandynawskie drewno (przede wszystkim sosnowe i świerkowe) charakteryzuje się doskonałymi parametrami wytrzymałości i gęstości. Dzięki starannie przeprowadzonej obróbce (w tym – suszeniu komorowemu oraz czterokrotnemu struganiu), materiał ten sprawdza się znakomicie do budowy nawet najbardziej wymagających konstrukcji szkieletowych oraz stabilnych i solidnych więźb dachowych.
Warto w tym miejscu zaznaczyć, że drewno pozyskane w północnych regionach Skandynawii charakteryzuje się dużo większą gęstością, twardością, sprężystością i wytrzymałością niż surowiec pochodzący z regionów południowych. Dobrze więc zwracać uwagę na dokładne pochodzenie sprowadzanego drewna. Spośród gatunków rodzimych, do produkcji drewna konstrukcyjnego stosuje się zazwyczaj drewno sosnowe, świerkowe, jodłowe oraz modrzewiowe. Spośród gatunków obcych, do celów budowlanych bywa natomiast wykorzystywana daglezja.
- Drewno sosnowe (PNSY) wyróżnia się doskonałą wytrzymałością, sprężystością oraz łatwością obróbki. Drewno sosnowe należy do kategorii drewna średnio ciężkiego o zabarwionej twardzieli. Charakteryzuje się ono czerwonobrązową twardzielą oraz żółtawobiałym, szerokim bielem. Przejście od drewna wczesnego do późnego odznacza się wyraźnie. Sęki rozmieszczone są równomiernie w okółkach, wyróżniając się barwą nieco ciemniejszą od otaczającego je drewna. W drewnie sosnowym często występują przeżywiczenia przysęczne o charakterystycznym, soczewkowym kształcie.
- Drewno świerkowe (PCAB) posiada bardzo dobre parametry wytrzymałości, ale wykazuje przy tym podatność na paczenie i pękanie. Drewno świerkowe należy do kategorii drewna lekkiego o niezabarwionej twardzieli. Charakteryzuje się ono jasnym, żółtawobiałym odcieniem. Przejście od drewna wczesnego do późnego jest łagodne. Sęki rozmieszczone są w okółkach, wyróżniając się barwą nieco ciemniejszą od otaczającego je drewna.
- Drewno jodłowe (ABAL) to drewno o dużej twardości oraz wysokiej sprężystości, ale mało podatne na impregnację. Drewno jodłowe należy do kategorii drewna lekkiego o niezabarwionej twardzieli. Charakteryzuje się ono brązoworóżowym odcieniem. Przejście od drewna wczesnego do późnego jest łagodne. Sęki rozmieszczone są dość nieregularnie.
- Drewno modrzewiowe (LADC) wykazuje bardzo dużą twardość oraz odporność na ogień. Drewno modrzewiowe należy do kategorii drewna umiarkowanie ciężkiego o zabarwionej twardzieli. Charakteryzuje się ono ciemnoczerwonobrązową twardzielą oraz żółtawym, wąskim bielem. Przejście od drewna wczesnego do późnego – gwałtowne. Sęki są liczne, nieregularnie rozmieszczone. Wyróżniają się ciemnobrunatną barwą.
- Drewno daglezjowe (PSMN) jest dość twarde i trudno zapalne. Odznacza się bardzo wysoką trwałością i odpornością na ścieranie, ale wykazuje przy tym podatność na pękanie. Drewno daglezjowe należy do kategorii drewna umiarkowanie lekkiego o zabarwionej twardzieli. Charakteryzuje się ono różowobrązową twardzielą oraz brązowawym, stosunkowo szerokim bielem. Przejście od drewna wczesnego do późnego odznacza się wyraźnie. Sęki rozmieszczone są w okółkach dość gęsto i regularnie.
Co do zasady, spośród gatunków drewna liściastego, w budownictwie wykorzystywane są głównie (i to w niewielkim stopniu) drewno dębowe oraz bukowe. Drewno dębowe jest twarde, bardzo wytrzymałe oraz odporne na ścieranie. Pod wpływem zmiennej wilgotności odznacza się ono jednak stosunkowo dużą podatnością na kurczenie i paczenie. W przemyśle budowlanym z drewna dębowego wykonuje się niewielkie elementy wymagające dużej twardości i odporności na ścieranie, między innymi kliny i różnego rodzaju podkładki.
Drewno bukowe jest ciężkie, twarde i łupliwe. Wykazuje ono także podatność na pękanie i paczenie oraz niewielką odporność na działanie owadów. W budownictwie wykorzystuje się je raczej rzadko.
Wartość drewna jako surowca konstrukcyjnego ilustruje znakomicie zestawienie go z innymi materiałami pod względem wartości współczynnika jakości wytrzymałościowej J. Współczynnik jakości wytrzymałościowej J informuje nas o długości pręta o przekroju 1 cm2, przy której ulegnie on zgnieceniu (w wyniku ściskania podłużnego) lub rozerwaniu przy określeniu samozerwalności elementu pod wpływem własnego ciężaru.
Na podstawie danych, które prezentujemy poniżej, można stwierdzić, że drewno najwyższej jakości (klasa wyborowa) dorównuje swoją wytrzymałością elementom metalowym, przewyższając przy tym znacznie wyroby z tworzyw sztucznych. Współczynnik jakości wytrzymałościowej wyraża się w metrach (m) lub kilometrach (km). I tak:
- współczynnik jakości wytrzymałościowej dla drewna sosnowego bez wad: 20 km,
- współczynnik jakości wytrzymałościowej dla polietylenu (23°C): 2,6 km,
- współczynnik jakości wytrzymałościowej dla polipropylenu (23°C): 4,5 km,
- współczynnik jakości wytrzymałościowej dla polichlorku winylu nieplastyfikowanego (23°C): 4 km,
- współczynnik jakości wytrzymałościowej dla stali ulepszonej: 16,5 km,
- współczynnik jakości wytrzymałościowej dla aluminium: 14 km.
Drewno klejone warstwowo
Oprócz drewna litego, do celów konstrukcyjnych znakomicie sprawdza się także drewno klejone warstwowo (tak zwana klejonka).
Do jego produkcji wykorzystuje się najczęściej wytrzymałe i odporne na wilgoć drewno świerkowe lub bardziej podatne na impregnację drewno sosnowe. Drewno klejone powstaje w wyniku sklejenia kilku warstw cienkich i giętkich lameli drewnianych o równoległym układzie włókien, wysuszonych do wilgotności 12% (+/- 2%).
Dzięki znakomitym parametrom wytrzymałości, a także stosunkowo niewielkiemu ciężarowi, znajduje ono zastosowanie nawet w najbardziej skomplikowanych i wymagających konstrukcjach nośnych (między innymi: w konstrukcjach dźwigarów dachowych, słupów, masztów, a nawet mostów) oraz w budowlach o dużej rozpiętości podpór.
Drewno klejone jest niezwykle plastyczne i wytrzymałe. Pozwala ono również znacząco ograniczyć zużycie materiału bez szkody dla bezpieczeństwa użytkowania konstrukcji. Opisując zalety drewna klejonego warstwowo, nie sposób nie wspomnieć o jego wysokiej odporności ogniowej. Elementy klejone o szerokości poniżej 12 cm określane są jako słabo rozprzestrzeniające ogień (grupa materiałów SRO). Elementy klejone o szerokości powyżej 12 cm funkcjonują z kolei jako nierozprzestrzeniające ognia (grupa materiałów NRO).
Drewno klejone powstaje z wykorzystaniem specjalistycznych mas klejowych: kleju melaminowego (najczęściej) lub kleju rezorcynowego (znacznie rzadziej). Co istotne, utwardzona masa klejowa charakteryzuje się takimi samymi parametrami z zakresu odporności na warunki atmosferyczne, wilgoć, ogień oraz gnicie jak samo drewno.
Zgodnie z klasyfikacją jakościowo-wytrzymałościową, drewno klejone podzielić możemy na dwie główne grupy:
- Drewno klejone warstwowo jednorodne (homogeneous) – klejonka o przekroju poprzecznym, na który składają się warstwy tarcicy tej samej klasy wytrzymałości oraz tego samego gatunku botanicznego (lub kombinacji różnych gatunków). Drewno klejone jednorodne dzieli się na siedem klas: GL20h, GL22h, GL24h, GL26h, GL28h, GL30h, GL32h (literka h odnosi się do angielskiego słowa homogeneous – jednorodny).
- Drewno klejone warstwowo mieszane (combined) – klejonka o przekroju poprzecznym, na który składają się warstwy tarcicy różnych klas wytrzymałości tego samego gatunku botanicznego lub kombinacji różnych gatunków. Warstwy zewnętrzne zbudowane są z lameli o większej wytrzymałości, podczas gdy warstwy wewnętrzne tworzone są z desek niższej jakości. Drewno klejone mieszane dzieli się, podobnie jak drewno jednorodne, na siedem klas: GL20c, GL22c, GL24c, GL26c, GL28c, GL30c, GL32c (literka c odnosi się do angielskiego słowa combined – mieszany).
W przypadku projektów wielkowymiarowych, najlepiej sprawdzi się drewno klejone w klasach GL28c oraz GL30c. W przypadku mniej wymagających elementów (więźb dachowych czy konstrukcji domów szkieletowych), wystarczające okażą się parametry tańszej i łatwiej dostępnej klasy GL24h.
Przygotowanie drewna konstrukcyjnego w tartaku
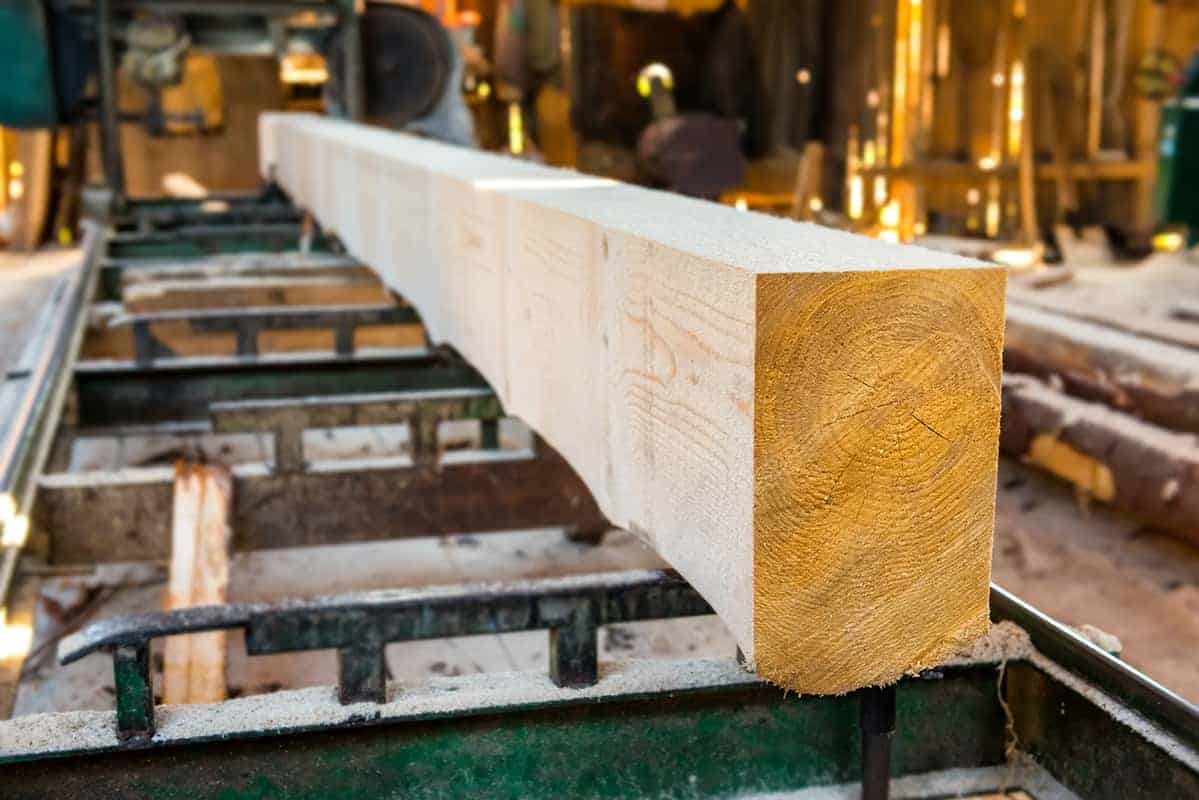
Przygotowanie konstrukcyjnego drewna w tartaku
Procesy obróbki drewna w tartaku podzielić możemy na trzy podstawowe etapy:
Suszenie drewna
Kupując drewno w tartaku, otrzymujemy najczęściej gotowy, odpowiednio wysuszony produkt. Suszenie odbywać się może na dwa sposoby:
- suszenie naturalne – wówczas schnie ono pod zadaszeniem na świeżym powietrzu od pół roku do kilku lat,
- suszenie komorowe – gdy suszenie odbywa się w specjalistycznych pomieszczeniach, w temperaturze około 70-75°C i regulowanej wilgotności. Proces suszenia komorowego trwa od kilku do kilkunastu godzin, gwarantując doskonałe parametry materiału.
Tarcie
Drewno przeznaczone do celów konstrukcyjnych musi zostać odpowiednio obrobione. Największą popularnością cieszy się drewno konstrukcyjne obrzynane o przekroju prostokątnym lub kwadratowym. Tartaki oferują ponadto czterostronne struganie drewna, w wyniku którego wszystkie powierzchnie materiału zostają wygładzone. Wśród usług dodatkowych, oferowanych za dodatkową opłatą wymienić można:
- przycinanie drewna na wymiar,
- frezowanie,
- ryflowanie,
- wycinanie wrębów,
- nawiercanie otworów.
Zabezpieczenie tarcicy
Odpowiednio przygotowane drewno konstrukcyjne nie musi być dodatkowo impregnowane. Wszystko zależy jednak od gatunku, klasy oraz zastosowanych metod produkcji. Dla zwiększenia trwałości i wytrzymałości materiału, wiele tartaków stosuje impregnację próżniową, głęboką lub – rzadziej – powierzchniową.
Klasy drewna konstrukcyjnego
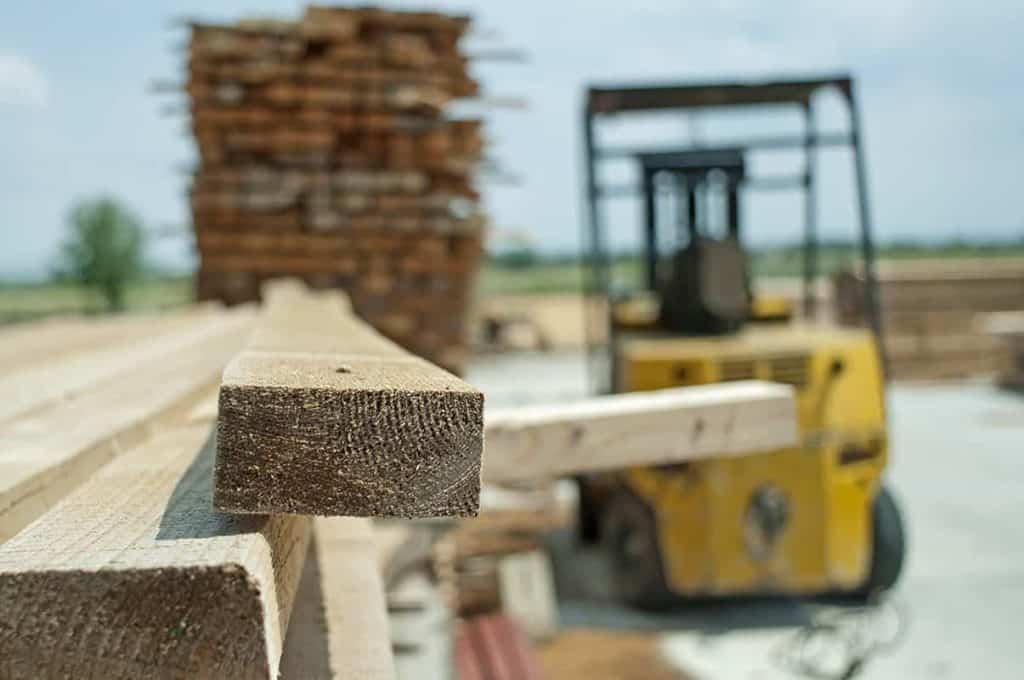
Klasy drewna na konstrukcje
Do celów konstrukcyjnych wykorzystuje się drewno lite oraz klejone warstwowo.
Drewno lite podzielone zostało na szereg klas wytrzymałości. Dla drewna iglastego wyróżnia się dwanaście klas od C14 do C50. Dla gatunków liściastych wprowadzono natomiast zaledwie osiem oznaczeń – od D18 do D70.
W obrębie drewna klejonego wyróżniamy z kolei siedem klas wytrzymałości: GL20, GL22, GL24, GL26, GL28, GL30, GL32, opisanych dodatkowo znacznikami „c” lub „h”. Znacznik „c” stosuje się w przypadku materiału mieszanego (combined), gdy został on wyprodukowany z tarcicy o różnej wytrzymałości. Znacznik „h” zarezerwowany jest natomiast dla drewna klejonego jednorodnego (homogeneous). W takim przypadku, materiał na całym swoim przekroju wykonany został z lameli o tych samych parametrach wytrzymałości.
Zgodnie z obowiązującymi normami, każda z klas drewna (czy to litego, czy klejonego) posiada ściśle określone parametry w zakresie wytrzymałości na zginanie, wytrzymałości na rozciąganie wzdłuż i w poprzek włókien, wytrzymałości na ściskanie wzdłuż i w poprzek włókien, wytrzymałości na ścinanie, średniego modułu sprężystości wzdłuż i w poprzek włókien oraz gęstości.
Kluczowe znaczenie dla określenia mechanicznych właściwości poszczególnych gatunków oraz klas drewna mają kierunek anatomiczny, wilgotność oraz liczba i rozmieszczenie różnego rodzaju wad strukturalnych.
Jednym z najważniejszych parametrów surowca jest jego wytrzymałość na ściskanie. Wytrzymałość na ściskanie zależy od ciężaru objętościowego drewna, jego wilgotności, stosunku zawartości drewna wczesnego do późnego w słojach rocznych, liczby, stanu i usytuowania sęków, kierunku przebiegu włókien oraz temperatury. Badania na próbkach małogabarytowych pokazują, że ogromne znacznie dla wytrzymałości drewna na ściskanie ma kierunek działania siły w stosunku do słojów i kierunku włókien.
I tak, największą wytrzymałością charakteryzują się próbki, w których siła działa stycznie względem słojów. Nieco gorszymi parametrami cechował się materiał ściskany w kierunku promieniowym. Najgorzej pod względem wytrzymałości na ściskanie wypadają natomiast te próbki, na które działały siły rozmieszczone pod kątem 45° do włókien. Zależności te są zawsze brane pod uwagę podczas wykonywania projektów obiektów drewnianych.
Cechą charakterystyczną drewna jako takiego jest wysoka wytrzymałość na rozciąganie wzdłuż włókien. Ujemny wpływ na wartość tego parametru posiadają sęki usytuowane na krawędziach elementów oraz ukośny przebieg włókien. Znacznie gorzej przedstawia się natomiast wytrzymałość drewna na rozciąganie w poprzek włókien – wynosi ono zazwyczaj od 2 do 7 % wytrzymałości na rozciąganie wzdłuż włókien (w zależności od gatunku drewna). Dlatego też, podczas projektowania konstrukcji drewnianej należy bezwzględnie unikać rozciągania elementów w kierunku prostopadłym do włókien.
Wytrzymałość drewna konstrukcyjnego na zginanie zależna jest od takich samych czynników jak w przypadku wytrzymałości na ściskanie i rozciąganie. Należy jednak pamiętać, że największe naprężenia w zakresie zginania elementów drewnianych występują na skraju przekroju. Wartości naprężeń na wysokości belki zmieniają się natomiast liniowo.
Co ciekawe, w elementach zginanych poddanych zbyt dużym obciążeniom, zerwaniu ulegają na ogół włókna rozciągane, a nie ściskane (mimo wysokiej wytrzymałości drewna na rozciąganie i jego stosunkowo niskiej wytrzymałości na ściskanie). Przyczyną tego stanu rzeczy jest przesuwanie się osi obojętnej w stronę naprężeń rozciągających pod wpływem nadmiernych sił ściskających.
Wytrzymałość drewna na zginanie zależy w dużej mierze od rodzaju i ilości wad drewna (między innymi: sęków oraz krzywoliniowego przebiegu włókien). Najlepszą wytrzymałością charakteryzują się elementy drewniane pozbawione sęków, o włóknach równoległych do krawędzi. Warto też zaznaczyć, że wytrzymałość drewna na zginanie zmniejsza się proporcjonalnie wraz ze wzrostem temperatury i wilgotności.
Kolejnym ważnym parametrem drewna jest jego odporność na ścinanie. O ścinaniu mówimy wówczas, gdy na dany element działają siły równoległe, skierowane przeciwnie w sposób prowadzący do wzajemnego przesunięcia obciążonych części. Z naprężeniami ścinającymi mamy do czynienia w przypadku połączeń na klocki czy wręby oraz w belkach zginanych. Naprężenia te wystąpić mogą zarówno wzdłuż, jak i w poprzek włókien.
Podczas określania parametrów wytrzymałościowych poszczególnych gatunków i klas drewna, dużą wagę przywiązuje się również do tak zwanego modułu sprężystości. Modułem sprężystości nazywamy współczynnik proporcjonalności między odkształceniem jednostkowym a naprężeniem, które je wywołuje. Moduły sprężystości drewna różnią się w zależności od kierunku (podłużnego, promienistego i stycznego). Parametr ten posiada decydujący wpływ na sztywność elementów w danych warunkach obciążenia. Uwzględnia się go więc zawsze podczas obliczania ugięć i odkształceń poszczególnych konstrukcji.
Poniżej przedstawiamy kompleksowe zestawienie najważniejszych parametrów wytrzymałościowych dla najczęściej wykorzystywanych klas drewna konstrukcyjnego litego (C24, C27 oraz C30) i klejonego (GL24h, GL28c oraz GL30c).
Drewno iglaste klasy C24 – podstawowe parametry:
- wytrzymałość na zginanie: 24 MPa,
- wytrzymałość na rozciąganie wzdłuż włókien: 14 MPa,
- wytrzymałość na rozciąganie w poprzek włókien: 0,5 MPa,
- wytrzymałość na ściskanie wzdłuż włókien: 21 MPa,
- wytrzymałość na ściskanie w poprzek włókien: 2,5 MPa,
- wytrzymałość na ścinanie: 2,5 MPa,
- średni moduł sprężystości wzdłuż włókien: 11 000 MPa,
- 5% kwantyl modułu sprężystości wzdłuż włókien: 7 400 N/mm2,
- średni moduł sprężystości w poprzek włókien: 370 MPa,
- średni moduł odkształcenia postaciowego: 690 N/mm2,
- gęstość charakterystyczna: 350 kg/m3,
- średnia gęstość: 420 kg/m3.
Drewno iglaste klasy C27 – podstawowe parametry:
- wytrzymałość na zginanie: 27 MPa,
- wytrzymałość na rozciąganie wzdłuż włókien: 16 MPa,
- wytrzymałość na rozciąganie w poprzek włókien: 0,4 MPa,
- wytrzymałość na ściskanie wzdłuż włókien: 22 MPa,
- wytrzymałość na ściskanie w poprzek włókien: 5,6 MPa,
- wytrzymałość na ścinanie: 2,8 MPa,
- średni moduł sprężystości wzdłuż włókien: 12 000 MPa,
- 5% kwantyl modułu sprężystości wzdłuż włókien: 7 700 N/mm2,
- średni moduł sprężystości w poprzek włókien: 400 MPa,
- średni moduł odkształcenia postaciowego: 720 N/mm2,
- gęstość charakterystyczna: 370 kg/m3,
- średnia gęstość: 450 kg/m3.
Drewno iglaste klasy C30 – podstawowe parametry:
- wytrzymałość na zginanie: 30 MPa,
- wytrzymałość na rozciąganie wzdłuż włókien: 18 MPa,
- wytrzymałość na rozciąganie w poprzek włókien: 0,6 MPa,
- wytrzymałość na ściskanie wzdłuż włókien: 23 MPa,
- wytrzymałość na ściskanie w poprzek włókien: 2,7 MPa,
- wytrzymałość na ścinanie: 3,0 MPa,
- średni moduł sprężystości wzdłuż włókien: 12 000 MPa,
- 5% kwantyl modułu sprężystości wzdłuż włókien: 8 000 N/mm2,
- średni moduł sprężystości w poprzek włókien: 430 MPa,
- średni moduł odkształcenia postaciowego: 750 N/mm2,
- gęstość charakterystyczna: 380 kg/m3,
- średnia gęstość: 460 kg/m3.
Drewno klejone GL24h – podstawowe parametry:
- wytrzymałość na zginanie: 24 N/mm2,
- wytrzymałość na rozciąganie wzdłuż włókien: 19,2 N/mm2,
- wytrzymałość na rozciąganie w poprzek włókien: 0,5 N/mm2,
- wytrzymałość na ściskanie wzdłuż włókien: 24 N/mm2,
- wytrzymałość na ściskanie w poprzek włókien: 2,5 N/mm2,
- wytrzymałość na ścinanie: 3,5 N/mm2,
- średni moduł sprężystości wzdłuż włókien: 11 500 N/mm2,
- 5% kwantyl modułu sprężystości wzdłuż włókien: 9 600 N/mm2,
- średni moduł sprężystości w poprzek włókien: 300 N/mm2,
- 5% kwantyl modułu sprężystości w poprzek włókien: 250 N/mm2,
- gęstość charakterystyczna: 385 kg/m3,
- średnia gęstość: 420 kg/m3.
Drewno klejone GL28c – podstawowe parametry:
- wytrzymałość na zginanie: 28 N/mm2,
- wytrzymałość na rozciąganie wzdłuż włókien: 19,5 N/mm2,
- wytrzymałość na rozciąganie w poprzek włókien: 0,5 N/mm2,
- wytrzymałość na ściskanie wzdłuż włókien: 24 N/mm2,
- wytrzymałość na ściskanie w poprzek włókien: 2,5 N/mm2,
- wytrzymałość na ścinanie: 3,5 N/mm2,
- średni moduł sprężystości wzdłuż włókien 12 500 N/mm2,
- 5% kwantyl modułu sprężystości wzdłuż włókien: 10 400 N/mm2,
- średni moduł sprężystości w poprzek włókien: 300 N/mm2,
- 5% kwantyl modułu sprężystości w poprzek włókien: 250 N/mm2,
- gęstość charakterystyczna: 390 kg/m3,
- średnia gęstość: 420 kg/m3.
Drewno klejone GL30c – podstawowe parametry:
- wytrzymałość na zginanie: 30 N/mm2,
- wytrzymałość na rozciąganie wzdłuż włókien: 19,5 N/mm2,
- wytrzymałość na rozciąganie w poprzek włókien: 0,5 N/mm2,
- wytrzymałość na ściskanie wzdłuż włókien: 24,5 N/mm2,
- wytrzymałość na ściskanie w poprzek włókien: 2,5 N/mm2,
- wytrzymałość na ścinanie: 3,5 N/mm2,
- średni moduł sprężystości wzdłuż włókien: 13 000 N/mm2,
- 5% kwantyl modułu sprężystości wzdłuż włókien: 10 800 N/mm2,
- średni moduł sprężystości w poprzek włókien: 300 N/mm2,
- 5% kwantyl modułu sprężystości w poprzek włókien: 250 N/mm2,
- gęstość charakterystyczna: 390 kg/m3,
- średnia gęstość: 430 kg/m3.
Właściwości fizykomechaniczne drewna sosnowego o wilgotności około 12-15% (wartości średnie):
- Gęstość: 520 kg/m3.
- Twardość Brinella: 40 MPa.
- Wytrzymałość na zginanie: 87 MPa.
- Wytrzymałość na rozciąganie: 104 MPa.
- Wytrzymałość na ściskanie: 47 MPa.
- Wytrzymałość na ścinanie: 10 MPa.
- Moduł sprężystości: 12 GPa.
Właściwości fizykomechaniczne drewna świerkowego o wilgotności około 12-15% (wartości średnie):
- Gęstość: 470 kg/m3.
- Twardość Brinella: 32 MPa.
- Wytrzymałość na zginanie: 66 MPa.
- Wytrzymałość na rozciąganie: 90 MPa.
- Wytrzymałość na ściskanie: 43 MPa.
- Wytrzymałość na ścinanie: 6,7 MPa.
- Moduł sprężystości: 11 GPa.
Właściwości fizykomechaniczne drewna jodłowego o wilgotności około 12-15% (wartości średnie):
- Gęstość: 450 kg/m3.
- Twardość Brinella: 30 MPa.
- Wytrzymałość na zginanie: 62 MPa.
- Wytrzymałość na rozciąganie: 84 MPa.
- Wytrzymałość na ściskanie: 40 MPa.
- Wytrzymałość na ścinanie: 5,1 MPa.
- Moduł sprężystości: 11 GPa.
Właściwości fizykomechaniczne drewna modrzewiowego o wilgotności około 12-15% (wartości średnie):
- Gęstość: 590 kg/m3.
- Twardość Brinella: 53 MPa.
- Wytrzymałość na zginanie: 84 MPa.
- Wytrzymałość na rozciąganie: 107 MPa.
- Wytrzymałość na ściskanie: 53 MPa.
- Wytrzymałość na ścinanie: 5 MPa.
- Moduł sprężystości: 12 GPa.
Właściwości fizykomechaniczne drewna daglezjowego o wilgotności około 12-15% (wartości średnie):
- Gęstość: 530 kg/m3.
- Twardość Brinella: 50 MPa.
- Wytrzymałość na zginanie: 71 MPa.
- Wytrzymałość na rozciąganie: 105 MPa.
- Wytrzymałość na ściskanie: 51 MPa.
- Wytrzymałość na ścinanie: 7,6 MPa.
- Moduł sprężystości: 8,97 GPa.
Klasy sortownicze a klasy wytrzymałościowe drewna krajowego
- Sosna zwyczajna o grubości większej lub równej 22 mm:
- KW – C35,
- KS – C24,
- KG – C20.
- Świerk pospolity o grubości większej lub równej 22 mm:
- KW – C30,
- KS – C24,
- KG – C18.
- Jodła pospolita o grubości większej lub równej 22 mm:
- KW – C22,
- KS – C18,
- KG – C14.
- Modrzew europejski o grubości większej lub równej 22 mm:
- KW – C35,
- KS – C30,
- KG – C24.
Wymiary tarcicy konstrukcyjnej
Ze względu na wymiary przekroju poprzecznego, wyróżniamy pięć rodzajów tarcicy konstrukcyjnej:
- deski,
- bale,
- łaty,
- krawędziaki,
- belki.
Tarcica obrzynana szorstka i strugana posiada grubość minimalną na poziomie 22 mm oraz minimalne pole przekroju poprzecznego o wartości 2000 mm2.
- Deski – wymiary:
- grubość (b): 22 mm ≤ b < 50 mm,
- stosunek szerokości (h) do grubości (b): h/b ≥ 2.
- Bale z drewna – wymiary:
- grubość (b): 50 mm ≤ b < 100 mm,
- stosunek szerokości (h) do grubości (b): h/b ≥ 2.
- Łaty – wymiary:
- grubość (b): 30 mm ≤ b < 100 mm,
- stosunek szerokości (h) do grubości (b): 1 ≤ h/b < 2.
- Belki drewniane – wymiary:
- grubość (b): b ≥ 100 mm,
- stosunek szerokości (h) do grubości (b): h/b ≥ 2.
Tarcica konstrukcyjna powinna wykazywać właściwą dokładność wymiarową. Wielkość dopuszczalnych odchyłek, czyli różnic między wymiarem rzeczywistym a docelowym określona została w normie PN-EN 336:2013-12. Warto w tym miejscu zaznaczyć, że norma PN-EN 336:2013-12 przyjmuje za punkt odniesienia wilgotność drewna na poziomie 20%. Jeśli mamy do czynienia z drewnem o wilgotności mniejszej lub większej niż 20%, powinniśmy przyjąć następujące założenia:
- w przypadku tarcicy o wilgotności w przedziale 20-30%, jej grubość i szerokość powinna wzrosnąć o 0,25% na każdy 1% wilgotności,
- w przypadku tarcicy o wilgotności poniżej 20%, jej grubość i szerokość powinna maleć o 0,25% na każdy 1% wilgotności.
Dla tarcicy konstrukcyjnej w I klasie tolerancji dopuszcza się następujące odchyłki wymiarów:
- dla tarcicy o grubości i szerokości ≤ 100 mm dopuszcza się maksymalną odchyłkę w zakresie od -1 do +3 mm,
- dla tarcicy o grubości i szerokości > 100 i ≤ 300 dopuszcza się maksymalną odchyłkę w zakresie od -2 do +4 mm,
- dla tarcicy o grubości i szerokości > 300 dopuszcza się maksymalną odchyłkę w zakresie od -3 do +5 mm.
Dla tarcicy konstrukcyjnej w II klasie tolerancji dopuszcza się następujące odchyłki wymiarów:
- dla tarcicy o grubości i szerokości ≤ 100 mm dopuszcza się maksymalną odchyłkę w zakresie od -1 do +1 mm,
- dla tarcicy o grubości i szerokości > 100 i ≤ 300 dopuszcza się maksymalną odchyłkę w zakresie od -1,5 do +1,5 mm,
- dla tarcicy o grubości i szerokości > 300 dopuszcza się maksymalną odchyłkę w zakresie od -2 do +2 mm.
Przedstawione powyżej maksymalne odchyłki wymiarowe dotyczą zarówno drewna litego, jak i drewna klejonego warstwowo.
Drewno KVH
Drewno KVH, czyli konstrukcyjne drewno lite (niem. Konstruktionsvollholz) to wysokiej jakości, nowoczesny materiał konstrukcyjny produkowany z drzew iglastych, przede wszystkim sosnowych, świerkowych oraz modrzewiowych. Aby zapewnić doskonałą stabilność kształtu i wymiarów (+/- 1 mm), drewno konstrukcyjne KVH jest suszone do wilgotności 15% +/- 3%. Wśród jego zalet wymienić należy także niewielką podatność na skręcenia oraz pęknięcia oraz możliwość łączenia go przy pomocy mikrowczepów w belki o długości nawet 13 m. Drewno konstrukcyjne KVH jest materiałem czterostronnie struganym o frezowanych krawędziach.
Wyróżniamy dwa rodzaje powierzchni drewna KVH:
- KVH-Si – przeznaczone dla konstrukcji widocznych, na przykład tarasów czy antresoli,
- KVH-NSi – przeznaczone dla konstrukcji niewidocznych (typowe drewno konstrukcyjne).
Ze względu na swoje liczne walory, drewno konstrukcyjne KVH znajduje powszechne zastosowanie w przemyśle budowlanym. Wykorzystuje się je, między innymi do:
- tworzenia drewnianych konstrukcji nośnych i usztywniających – sprawdza się znakomicie w produkcji belek wsporników, słupów, krokwi, płatwi oraz różnego rodzaju elementów dachowych, stropowych oraz ściennych obiektu,
- tworzenia konstrukcji, których przeznaczenie uniemożliwia korzystanie z chemicznych preparatów ochrony drewna,
- produkcji różnego rodzaju elementów konstrukcyjnych wymagających dużej stabilności wymiarowej,
- tworzenia widocznych elementów konstrukcji o wysokich walorach estetycznych (w przypadku drewna KVH-Si).
Drewno KVH – podstawowe parametry:
- klasa wytrzymałości: C24,
- wilgotność: 15% +/- 3%,
- gęstość: 350 kg/m3,
- wytrzymałość na zginanie: 24 MPa,
- wytrzymałość na rozciąganie wzdłuż włókien: 14 MPa,
- wytrzymałość na rozciąganie w poprzek włókien: 0,4 MPa,
- wytrzymałość na ściskanie wzdłuż włókien: 21 MPa,
- wytrzymałość na ściskanie w poprzed włókien: 2,5 MPa,
- średni moduł sprężystości: 11 000 MPa,
- pęcznienie i kurczenie: 0,24% na 1% zmiany wilgotności.
Drewno konstrukcyjne na dach
Do najczęściej wykorzystywanych konstrukcji drewnianych należą bez wątpienia wiązary dachowe, czyli konstrukcje przenoszące obciążenia z połaci dachowych na podpory. W zależności od wybranego typu dachu, jego układ nośny składać się może z belek, krokwi, płatwi, jętek, tężników, etc.
Obecnie najczęściej spotykamy dachy zbudowane z wiązarów:
- krokwiowych,
- krokwiowo-jętkowych,
- płatwiowo-kleszczowych,
- płatwiowych,
- mansardowych,
- wieszarowych,
- rozporowych.
Do budowy dachów wykorzystuje się najczęściej wysokiej jakości drewno konstrukcyjne poddane procesom suszenia oraz czterokrotnego strugania. Najlepsze rezultaty uzyskuje się w wyniku suszenia komorowego prowadzonego w warunkach kontrolowanej temperatury (70-75°C) i wilgotności. Wysoka temperatura pozwala wyjałowić drewno i oczyścić je z niepożądanych mikroorganizmów. Dzięki temu, materiał nie pęka i nie paczy się, uzyskując ponadto wysoką odporność na działanie grzybów, pleśni oraz różnego rodzaju insektów. Proces czterokrotnego strugania zapewnia natomiast zwiększoną odporność ogniową drewna – gładka powierzchnia utrudnia zapłon oraz swobodne rozprzestrzenianie się ognia.
Impregnacja drewna konstrukcyjnego
Suszenie komorowe drewna do wilgotności poniżej 20% pozwala praktycznie zrezygnować z impregnacji. Proces ten prowadzi bowiem do wyjałowienia materiału i oczyszczenia go z wszelkich organizmów, w tym owadów. Niski poziom wilgotności uzyskany podczas suszenia oraz gładka powierzchnia elementów czterokrotnie struganych uniemożliwiają insektom ponowne zagnieżdżenie się w materiale. Suche drewno konstrukcyjne nie sprzyja także rozwojowi niszczących grzybów i pleśni. Ponadto, dzięki procesowi czterokrotnego strugania, wygładzona powierzchnia drewna opóźnia i utrudnia zapłon materiału, gwarantując konstrukcji zwiększoną odporność ogniową.
Jeśli jednak decydujemy się na dodatkowe zabezpieczenie drewna przy pomocy specjalistycznych preparatów, możemy to zrobić, wykorzystując jedną z trzech metod impregnacji:
- powierzchniową – najmniej skuteczną, wykonywaną poprzez malowanie, krótkotrwałe zanurzanie lub natryskiwanie drewna roztworem impregnatu,
- głęboką – wykonywaną poprzez wielodniowe moczenie drewna w wybranym impregnacie,
- próżniową (ciśnieniową) – najbardziej skuteczną, wykonywaną metodą ciśnieniową w specjalistycznym autoklawie.
Certyfikacja drewna konstrukcyjnego
Decydując się na zakup drewna konstrukcyjnego, powinniśmy zwracać szczególną uwagę na charakterystyczny symbol CE. Zgodnie z normami obowiązującymi w całej Unii Europejskiej, producenci drewna konstrukcyjnego mają bowiem obowiązek uzyskać prawo do certyfikacji swoich wyrobów.
Sprzedaż materiału bez certyfikacji wiąże się z wysokimi karami finansowymi nakładanymi przez Inspektorat Nadzoru Budowlanego. Zakup i korzystanie z takiego drewna stanowi natomiast ogromne ryzyko dla bezpieczeństwa wszystkich jego użytkowników.
Co oznacza symbol CE? Jest to europejski znak jakości (Conformité Européenne), stosowany jako dowód zgodności wyrobów z normami Unii Europejskiej dotyczącymi bezpieczeństwa użytkowania, ochrony zdrowia oraz ochrony środowiska.
Prawo do certyfikacji drewna konstrukcyjnego uzyskuje się poprzez wdrożenie systemu Zakładowej Kontroli Produkcji (ZKP) umożliwiającego stałą ocenę zgodności produkowanych materiałów z dyrektywami Unii Europejskiej. ZKP zobowiązuje producentów do prowadzenia szczegółowej dokumentacji oraz stałej wewnętrznej kontroli jakości materiału pod względem jego zgodności z obowiązującymi normami.
Prawo do certyfikacji uzyskują producenci dbający o prawidłowe sortowanie wytrzymałościowe drewna konstrukcyjnego, niezależnie czy proces ten przeprowadzany jest metodą wizualną, czy też z wykorzystaniem nowoczesnego sprzętu automatycznego. Podczas sortowania, materiał przypisywany jest do jednej z trzech klas sortowniczych:
- Wyborowej (KW).
- Średniej (KS).
- Niższej (KG).
Oznaczenie CE może zostać umieszczone na produktach zatwierdzonych w procesie oceny zgodności. Symbol musi być czytelny i widoczny. Kupując drewno certyfikowane, mamy pewność, że parametry materiału kwalifikują go do zastosowań konstrukcyjnych.
Drewno konstrukcyjne cena
Cena drewna konstrukcyjnego zależy od jego gatunku, klasy, zastosowanych metod obróbki, wymiarów oraz dostępności. Najlepszą dostępnością charakteryzuje się drewno lite iglaste (przede wszystkim świerkowe, nieco rzadziej – sosnowe) w klasach C24 i C27 oraz drewno klejone w klasie GL24h. Generalnie, cena wysokiej jakości drewna konstrukcyjnego w podanych wyżej klasach zaczyna się od 1900 zł/m3.
FAQ
Ile kosztuje drewno konstrukcyjne?
Cena drewna konstrukcyjnego zależy od jego gatunku, klasy, zastosowanych metod obróbki, wymiarów oraz dostępności. Najlepszą dostępnością charakteryzuje się drewno lite iglaste (przede wszystkim świerkowe, nieco rzadziej - sosnowe) w klasach C24 i C27 oraz drewno klejone w klasie GL24h. Cena wysokiej jakości drewna konstrukcyjnego w podanych wyżej klasach waha się w granicach 900-1500 zł/m3.
Jakie drewno nadaje się na konstrukcję dachu?
Do budowy dachów wykorzystuje się najczęściej wysokiej jakości drewno konstrukcyjne poddane procesom suszenia oraz czterokrotnego strugania. Najlepsze rezultaty uzyskuje się w wyniku suszenia komorowego prowadzonego w warunkach kontrolowanej temperatury (70-75°C) i wilgotności.
Czy drewno konstrukcyjne musi zostać zaimpregnowane?
Suszenie komorowe drewna do wilgotności poniżej 20% pozwala praktycznie zrezygnować z impregnacji.