W dużym uproszczeniu prefabrykacja konstrukcji drewnianych polega na tworzeniu gotowych elementów budowlanych, z których powstają następnie konstrukcje budynków. Technologia ta kojarzy się przede wszystkim z przetwórstwem betonu z którego powstają cegły, bloczki czy pustaki.
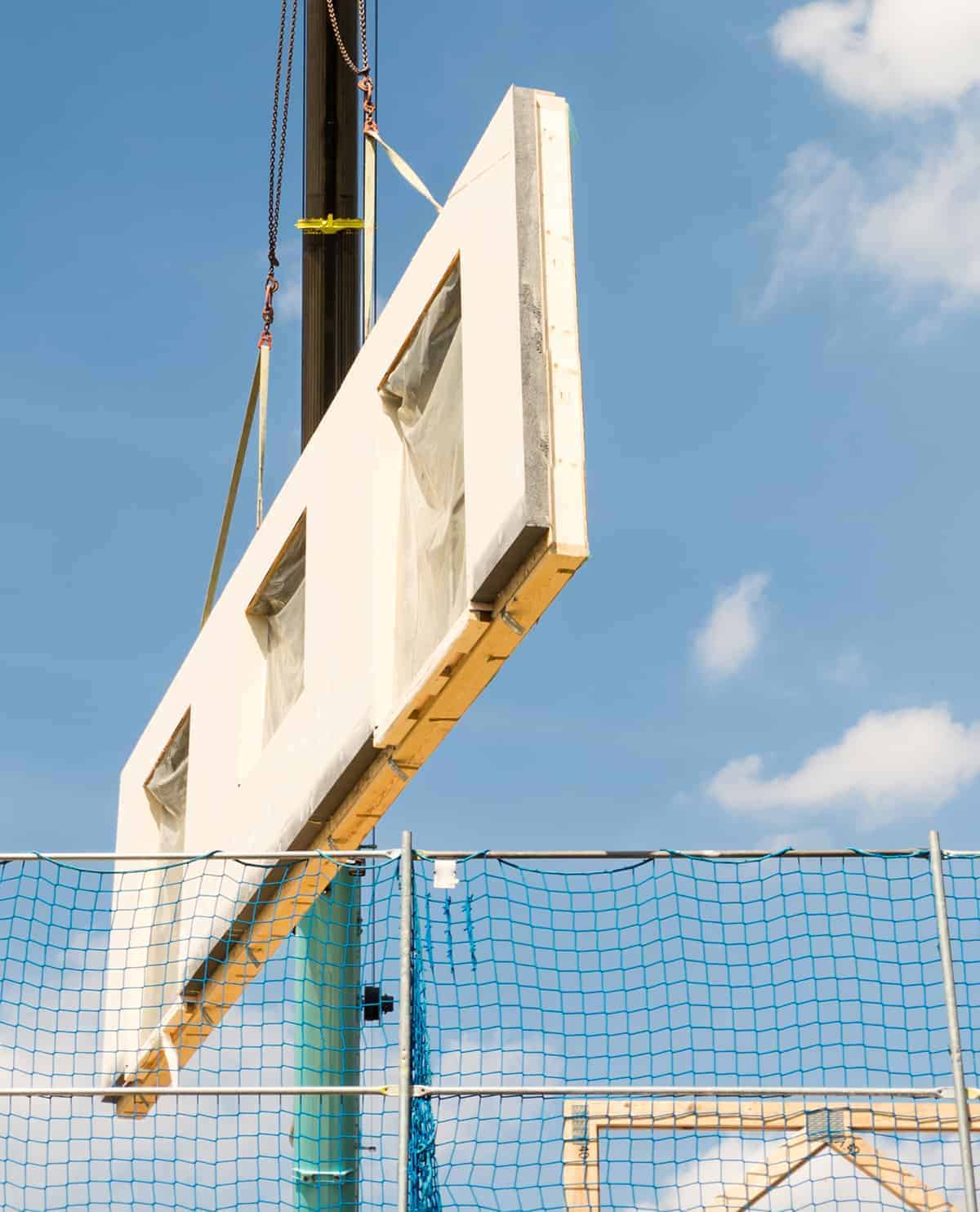
Prefabrykacja
Prefabrykaty mogą być jednak produkowane także z drewna. Nowoczesna technologia prefabrykacji MiTek pozwala na uzyskanie znakomitych parametrów jakościowych oraz wysokiej estetyki takich wyrobów. Czym jest prefabrykacja i jakie ma zastosowanie we współczesnym budownictwie odpowiemy w tym artykule.
Na czym polega prefabrykacja?
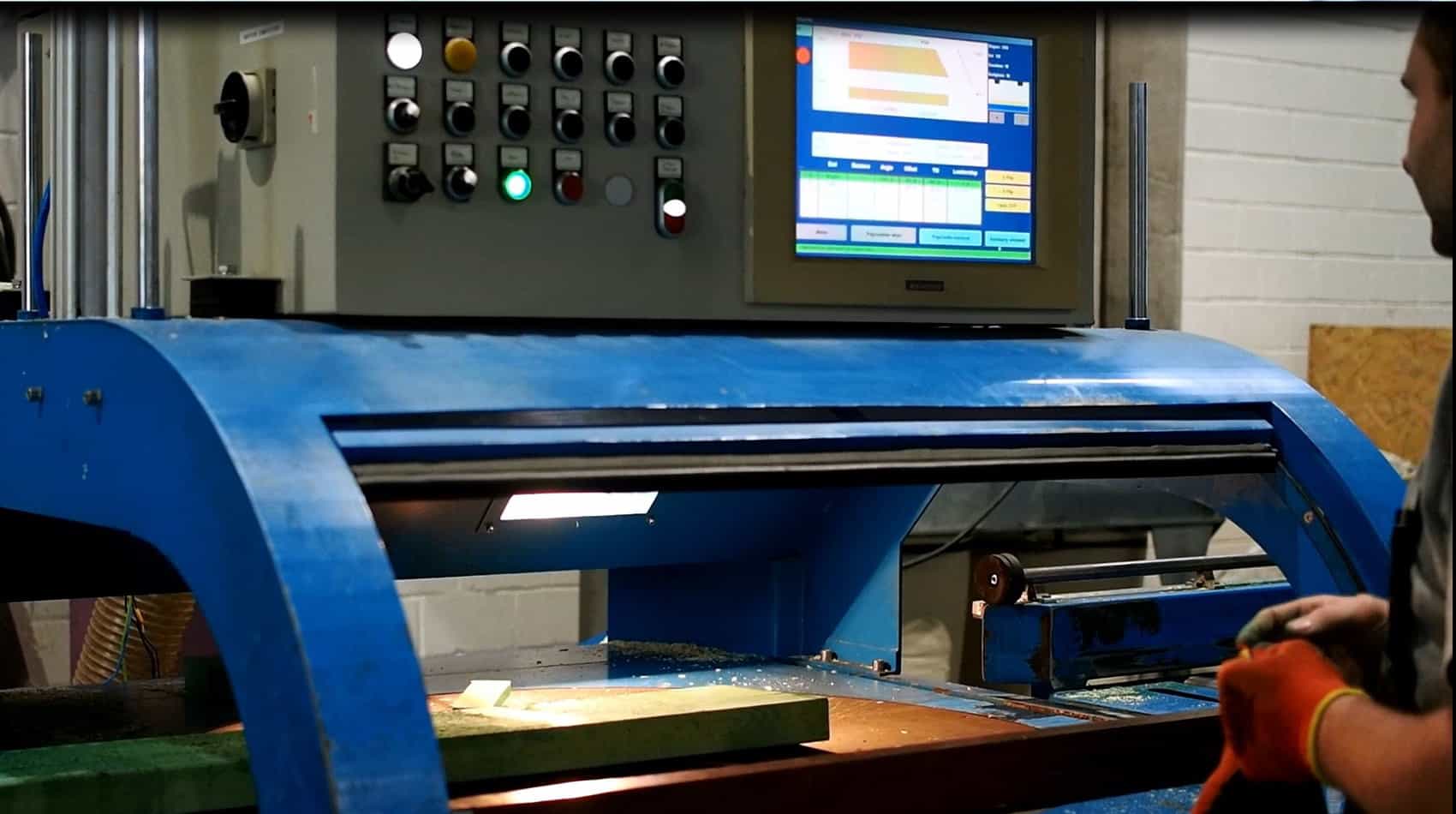
Na czym polega prefabrykacja?
Prefabrykacja to technologia, która polega na wytwarzaniu wielkowymiarowych elementów budowlanych poza miejscem budowy. Wyroby te powstają w zakładzie prefabrykacji, a do ich produkcji wykorzystywane są różne metody przemysłowe. Prefabrykaty już od wielu lat pozostają przejawem nieustannego postępu technologicznego w budownictwie. Znacząco bowiem upraszczają złożony proces budowy. Pozwalają na przeniesienie znacznej jego części do zewnętrznych zakładów, co wiąże się z wieloma zaletami dla Inwestora.
Zastosowanie konstrukcji prefabrykowanych ogranicza prace na budowie praktycznie wyłącznie do montażu gotowych elementów. Dzięki prefabrykacji można znacząco przyspieszyć całą budowę oraz w dużym stopniu uniezależnić ją od warunków pogodowych. Pozwala ona na podniesienie precyzji wymiarowej elementów montowanej konstrukcji obiektu oraz ich jakości. Technologia prefabrykacji opiera się także na wdrażaniu różnych przydatnych rozwiązań, które dodatkowo ułatwiają realizację pomniejszych prac, m.in. wykonanie otworów technologicznych, mocowanie części konstrukcji czy podwieszanie instalacji.
Rozpowszechnienie technologii prefabrykacji wynika z nieustannego dążenia do redukcji kosztów budowy, przede wszystkim poprzez eliminację dość drogiego stropu betonowego.
Prefabrykaty zyskują popularność także z uwagi na wyjątkowo szybkie tempo budowy. Na powodzenie tego rozwiązania wpływają również inne czynniki. W zależności od wielkości i technologii budynku, montowanie z zastosowaniem prefabrykatów ukończyć można nawet w ciągu jednego dnia. W przypadku większej budowy okres ten nie powinien przekroczyć tygodnia. Budynek z prefabrykatów jest następnie sprawnie i zgodnie z planem wykańczany.
Technologia ta w dużym stopniu ogranicza ilość śmieci i odpadów pozostawionych na placu budowy. Wynika to z faktu obecności w jej obrębie wyłącznie niezbędnych w danym czasie elementów. Wszystkie prefabrykaty przygotowane są w określonych wymiarach i nie wymagają żadnej dodatkowej obróbki.
Dodatkową zaletą jest fakt, że w prefabrykacji w dużym stopniu wyklucza się metody mokre. Mogą one przyczyniać się do przerw technologicznych oraz uzależnienia przebiegu prac od warunków atmosferycznych, co niepotrzebnie wydłuża czas budowy.
Firmy zajmujące się budową domów z prefabrykatów z reguły posiadają duże doświadczenie z pracy z takimi produktami. Najczęściej są to doskonale przeszkolone ekipy, a nierzadko pracownicy autoryzowanych marek. Jasna instrukcja pozwala im na sprawną realizację kolejnych etapów budowy krok po kroku, jak przy układaniu klocków.
W przypadku domów prefabrykowanych gotowe elementy dają możliwość zaoszczędzenia na grubości ścian, która w ich przypadku zazwyczaj nie przekracza 30 cm. W rezultacie uzyskać można większą powierzchnię użytkową pomieszczeń budynku w porównaniu do technologii murowanej. Technologia prefabrykacji pozwala przy tym na wykonanie praktycznie dowolnego projektu domu, niezależnie od jego standardu. Może to być budynek zarówno typowy i przygotowany w oparciu o gotowy koncept, jak i skomplikowany oraz opracowany całkowicie indywidualnie.
Technologia prefabrykowana coraz powszechniej wykorzystywana jest do stawiania domów ze szkieletem drewnianym. Rozwiązanie to dodatkowo skraca czas budowy i ogranicza ryzyko popełnienia trudnych w naprawie błędów wykonawczych. Wiele firm udziela na drewniane konstrukcje nawet kilkudziesięcioletniej gwarancji oraz długiej rękojmi na wykonawstwo i zastosowane materiały.
W budowie drewnianych domów prefabrykowanych stosuje się elementy wykonane z certyfikowanej tarcicy i drewna klejonego. Materiał tego typu powstaje poprzez wycięcie wszystkich wadliwych obszarów z wysuszonych belek, które są następnie sklejane oraz poddawane ostruganiu. Później konieczne jest ich ponowne podzielenie na krótsze odcinki.
Z uwagi na długość naczep pojazdów ciężarowych, najczęściej mają maksymalnie kilkanaście metrów. Tak przygotowane drewno jest odporne na wilgoć, wytrzymałe mechanicznie oraz stabilne pod względem wymiarowym. W drewnianych domach najczęściej stosuje się drewno świerkowe, poddane suszeniu komorowemu w wilgotności na poziomie kilkunastu procent.
W przypadku prefabrykatów drewnianych bardzo duże znaczenie ma technologia suszenia surowca. Zastosowanie metody komorowej niweluje ryzyko pozostawienia zarodników grzybów i pleśni. Proces suszenia jest również w stanie zabić larwy owadów oraz powstrzymać naturalne sinienie drewna. Poddanie surowca działaniu temperatury 60 stopni Celsjusza usuwa wszelkiego rodzaju naturalne substancje, które stosunkowo szybko mogłyby stać się pożywką dla szkodników.
Drewno konstrukcyjne strugane jest z każdej strony. Jego krawędzie poddawane są też fazowaniu, co lepiej uodparnia elementy na działanie ognia. Płomienie ślizgają się po gładko ostruganej powierzchni, co w dużym stopniu utrudnia zapłon i zwiększa ochronę przeciwogniową całej konstrukcji.
Zastosowane do prefabrykacji drewno może mieć różną klasę jakości. Określa się ją w zależności od zakresu dopuszczalnych wad. Najczęściej stosowane jest drewno konstrukcyjne C24. Wytrzymałość na obciążenia dla tej klasy przyjmuje się na podstawie obliczeń statycznych konstrukcji budynku.
Dla prefabrykatów drewnianych bardzo istotne jest także dobre zabezpieczenie przed wilgocią. Fundamenty konstrukcji muszą dysponować szczelną izolacją poziomą. Wysoką szczelność są w stanie zapewnić jedynie certyfikowane papy.
Prawidłowo wykonany dom drewniany w technologii prefabrykacji może mieć parametry energooszczędności nieustępujące domom pasywnym.
Nie bez znaczenia pozostaje coraz większa uniwersalność tego rozwiązania. Producenci prefabrykatów w ostatnich latach znacząco wzbogacili swoje oferty. Inwestorzy mają do wyboru nie tylko typowe projekty domów, ale też szeroki zakres usług dodatkowych. Dom w technologii prefabrykacji wybudować można zarówno do stanu surowego otwartego, jak i pod klucz.
Na życzenie Klienta budynek wyposażany może zostać w rekuperator, pompę ciepła, kolektory słoneczne oraz niezbędne dla ich działania instalacje. Technologia prefabrykacji daje też spore możliwości w kwestii wykańczania wnętrz domu. Przekłada się to na swobodę w aranżacji. Coraz częściej tworzone są gotowe wzory detali, np. dowolnie zestawianych ze sobą modułów ścianek, podświetlanych sufitów czy wnęk. Inwestor może w ten sposób wykreować odpowiedni dla swoich preferencji projekt wnętrza, a przy tym czerpać wiele korzyści z zastosowanej technologii budowy.
Zastosowanie drewnianych elementów prefabrykowanych
Istnieje wiele zastosowań prefabrykowanych elementów drewnianych w obiektach budowlanych. Zainteresowanie prefabrykacją wynika z dużej popularności budownictwa nowoczesnego i energooszczędnego. Technologia ta pozwala na tworzenie konstrukcji różnego typu.
W ten sposób powstają dachy jednospadowe, mansardowe, kopertowe czy łukowe. Elementy prefabrykowane znajdują szerokie zastosowanie w budynkach mieszkalnych, produkcyjnych, magazynowych, czy rolniczych. Stosowane są także w formie nadbudowy na płaski dach. Podstawę stanowią budynki wykonane w systemie płytowym.
Technologia ta często nazywana jest budownictwem fińskim lub szwedzkim. Poza płytami o długości do kilkunastu metrów, produkuje się również konstrukcje ścian, dachów i stropów na siatkach modularnych o odpowiednim rozstawie. Płyty ścienne posiadają wysokość równą wysokości całkowitej wybranej kondygnacji. Elementy te pozwalają na łatwe zamontowanie stolarki drzwiowej i okiennej każdego typu.
Konstrukcja dachu w przypadku technologii płytowej wykonywana jest z drewnianych dźwigarów kratowych.
Innym rodzajem konstrukcji drewnianej prefabrykowanej są domy modułowe. Powstają one z wielkich, przestrzennych struktur modułowych. Konstrukcja tego typu opiera się na pionowych i poziomych sztywnych ramach drewnianych, które należy ze sobą połączyć. Elementy mogą w być otwartej z jednej strony lub w całości zamknięte. Te pierwsze powalają na utworzenie dużych pomieszczeń po dodaniu do siebie.
W konstrukcjach modułowych poziom prefabrykacji jest bardzo wysoki. Tak wykonane obiekty posiadają gotowe podłogi i ściany, a także wbudowane niezbędne instalacje. Od zewnątrz do elementów konstrukcyjny przymocowywane są płyty elewacyjne, a od wewnątrz płyty gipsowo-kartonowe. Między elementami szkieletu nośnego umieścić można instalacje i ocieplenie. Na plac budowy przewieźć da się nawet komplety segment, z zamontowanymi meblami oraz położoną wykładziną.
Drewniany szkielet zbudowany jest z belek i słupów, które następnie są uzbrajane.
Prefabrykacja otwarta
W zależności od stopnia zabudowy, technologia prefabrykacji domów drewnianych rozróżniona może być na otwartą i zamkniętą. Najpopularniejsza w Polsce jest odmiana otwarta, na którą składa się drewniany szkielet konstrukcji pokryty płytą drewnopochodną – np. wiórową.
Z przygotowanych w ten sposób prefabrykatów montuje się następnie podstawowe elementy konstrukcyjne budynku, takie jak dachy, ściany i stropy.
Kiedy montaż konstrukcji zostanie zakończony, przeprowadzane jest wykańczanie budynku od zewnątrz. Na tym etapie układa się pokrycie dachowe, wykonuje elewację oraz wstawia okna i drzwi.
Po doprowadzeniu budynku do stanu surowego zamkniętego, rozpoczynają się roboty wykończeniowe. Obejmują one montaż poszczególnych instalacji, a także układanie izolacji akustycznej w ścianach wewnętrznych oraz izolacji cieplnej w ścianach zewnętrznych.
Na kolejnym etapie ściany zamyka się odpowiednim poszyciem od wewnątrz, zwykle płytami gipsowo-włóknowymi lub gipsowo-kartonowymi.
Prefabrykacja zamknięta
Prefabrykacja zamknięta jest bardziej zaawansowana w porównaniu do otwartej, jednak jej stopień może być różny. Z reguły ściany wypełnione izolacją cieplną wymagają całościowego wykończenia w fabryce. Od strony zewnętrznej stosuje się płytę gipsowo-kartonową, a od zewnętrznej specjalną warstwę elewacyjną.
Więźba dachowa również jest prefabrykowana, a jej elementy należy dostosować do pokrycia dachowego i zamontować na budowie. W przypadku najbardziej zaawansowanych systemów prefabrykacji, na plac budowy dostarcza się ściany całkowicie wyposażone w drzwi, okna i rolety. Wykończone są zarówno od wewnątrz, jak i od zewnątrz. Podobnie wygląda to w przypadku stropów oraz części połaci dachu z pokryciem gotowym. Tak przygotowane elementy zamontować da się nawet w kilka lub kilkanaście godzin.
Prefabrykacja modułowa
Jeszcze wyższym poziomem zaawansowania charakteryzuje się prefabrykacja modułowa. W tym przypadku w fabryce przygotowywane są przestrzenne elementy domu, a nierzadko nawet całe małogabarytowe budynki.
Warianty mniej zaawansowane pozwalają na złożenie kolejnych pomieszczeń obiektu. Bardziej zaawansowane moduły mogą obejmować kompletne kondygnacje, o ile budynek jest nieduży. Konstrukcja dachu często stanowi jeden moduł.
Taki dom da się zmontować w zaledwie kilka godzin. Drewniane domy prefabrykowane stawia się na gotowym fundamencie, najczęściej w postaci płyty fundamentowej. Jego cechą wyróżniającą powinna być duża dokładność wykonania, celem zapewnienia płaskości i równości powierzchni płyty. Ewentualne odchylenia od poziomu nie powinny przekraczać 2 mm na całej długości zewnętrznej ściany obiektu. Niedoskonałości fundamentu nie mogą utrudnić montażu prefabrykatów, dlatego całość prac powinna wykonać doświadczona ekipa.
Prefabrykowane budownictwo szkieletowe charakteryzuje się małą pojemnością cieplną. Wynika to z obecności izolacji termicznej zastosowanej w przegrodach, która z kolei posiada niski współczynnik bezwładności cieplnej. Tak materiał nie jest w stanie umożliwić akumulacji ciepła, przez co dom drewniany szybko się wychładza.
Istnieją różne metody zwiększania akumulacyjności ciepła prefabrykowanych domów o szkieletowej konstrukcji drewnianej. Należy do nich możliwość wyłożenia wnętrza grubą okładziną drewnianą wnętrza budynku oraz ścian wewnętrznych i zewnętrznych. Brak dostatecznej pojemności cieplnej przegród rekompensuje też wodne ogrzewanie podłogowe. W takim przypadku to nie ściany, a betonowa wylewka będzie odpowiadać za akumulację ciepła.
Nie bez znaczenia pozostaje jednak współczynnik przenikalności cieplnej. W przypadku ścian i dachu obiektu zbudowanego w takiej technologii, U wynosi poniżej 0,17 W/(m2 K). W praktyce do ogrzania domu potrzeba stosunkowo niedużo energii cieplnej. Po uruchomieniu ogrzewania nawet wychłodzony budynek zdoła się ocieplić po kilkunastu minutach. W lecie dom nagrzewa się przede wszystkim przez okna, ponieważ dach i ściany są wystarczająco izolowane. Niewielka bezwładność cieplna ułatwia chłodzenie budynku. W zupełności wystarczy zamontowanie rolet okiennych.
Ważną kwestią w technologii prefabrykowanego szkieletu drewnianego jest układ warstw ścian. Zapewnia on budynkowi trwałość, a także energooszczędność.
Poszczególne warstwy ścian spełniają przypisane do nich funkcje. W przypadku pominięcia którejkolwiek z nich, utracić można cenne właściwości ściany.
- Standardowy układ warstw ściany zewnętrznej rozpoczyna się od płyty gipsowo-kartonowej lub gipsowo-włóknowej, która stanowi wewnętrzną warstwę wykończeniową.
- Następnie stosowana jest paroizolacja. Jej celem jest ograniczenie przepływu wilgoci do wnętrza ściany, celem ochrony izolacji i konstrukcji budynku przed zawilgoceniem.
- Po paroizolacji układa się izolację cieplną, której minimalna grubość powinna wynieść 140 mm. Najczęściej stosuje się w tym celu wełnę mineralną. Sporą popularność zyskuje też izolacja cieplna z włókien celulozowych.
- Kolejna warstwa to poszycie zewnętrzne. Jej zadaniem jest usztywnienie konstrukcji szkieletu ścian. Spełnia ona również funkcję izolacji akustycznej dla ściany zewnętrznej oraz podkładu pod materiały elewacyjne. Najczęściej poszycie zewnętrzne powstaje z płyt drewnopochodnych o wysokiej odporności na wilgoć.
- Kolejna warstwa to wiatroizolacja. Chroni płyty poszycia przed wilgocią zewnętrzną, a także zapewnia odprowadzanie nagromadzonej wewnątrz ściany pary wodnej. Chroni również budynek przed wychłodzeniem powodowanym działaniem wiatru.
- Na koniec stosuje się wykończenie zewnętrzne ściany. Najczęściej jest to oblicówka drewniana lub siding winylowy, ewentualnie obmurówka z cegieł klinkierowych lub tynk na styropianie.
Elementy przygotowane do montażu posiadają specjalne kanały instalacyjne. Ich obecność znacząco ułatwia podłączenie rur wodno-kanalizacyjnych, a także prowadzenie przewodów elektrycznych.
Warto wspomnieć także o stropach. Ich konstrukcja obejmuje belki drewniane lub prefabrykaty stropowe. Najczęściej wypełnia się je wełną mineralną, która ma spełniać funkcję izolacji akustycznej. Elementy obijane są od góry płytami drewnopodobnymi, a od dołu gipsowo-kartonowymi lub gipsowo-włóknowymi. Dużą popularnością cieszy się izolacja nakrokwiowa.
Technologia prefabrykacji MiTek
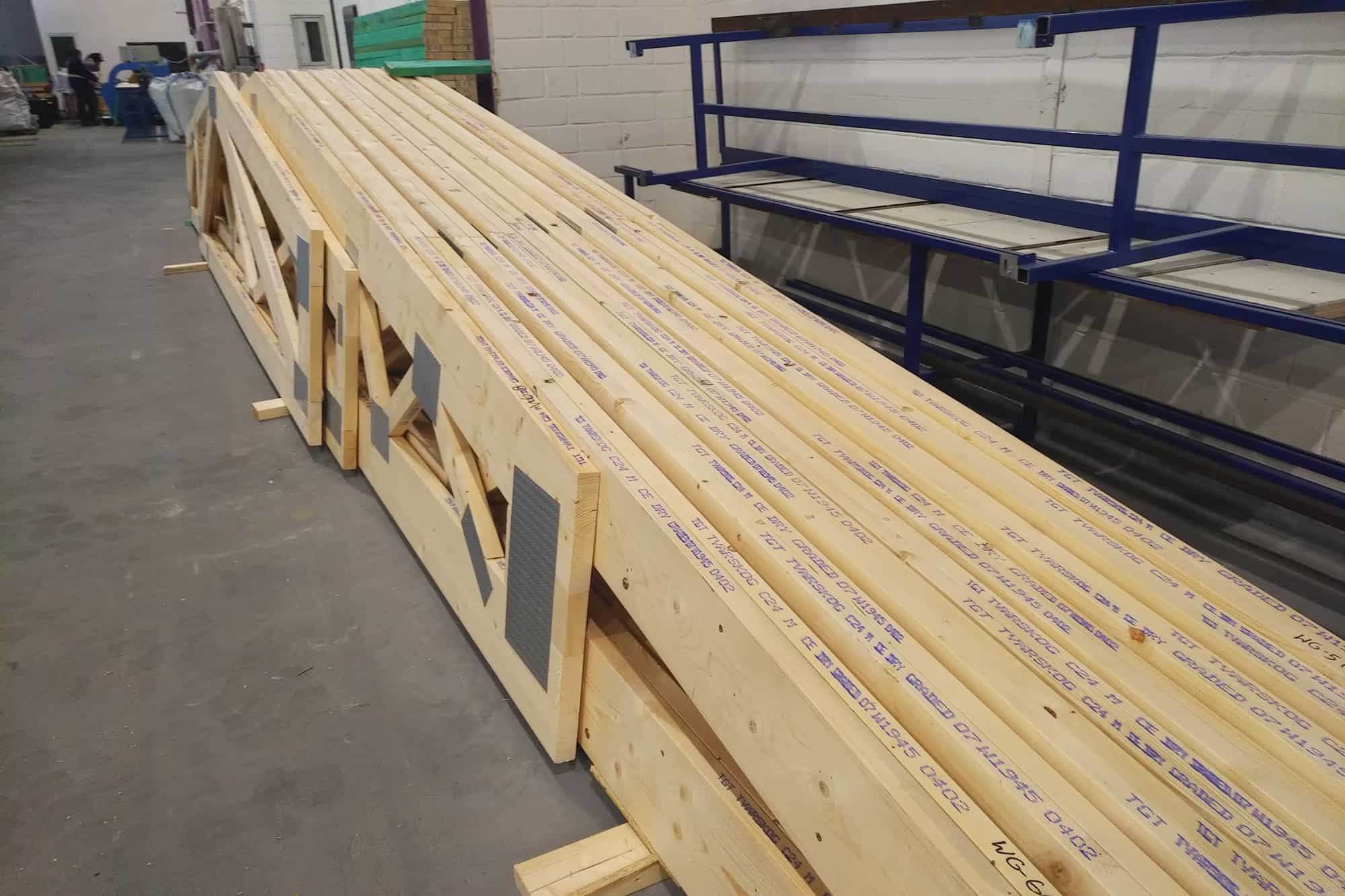
Technologia prefabrykacji MiTek
Drewniany dom prefabrykowany jest ekologiczny i energooszczędny. Konstrukcje tego typu zapewniają korzystny dla człowieka mikroklimat. Za sprawą zastosowania naturalnego surowca, wyróżniają się wysoką estetyką wykonania.
Z tych względów prefabrykowane konstrukcje drewniane powszechnie wykorzystywane są do realizacji różnych prac budowlanych. Posiadają jednak pewne ograniczenia, które na ogół powodowane są relatywnie kiepskimi połączeniami. Rozwój technologii pozwolił jednak na utworzenie nowoczesnych rozwiązań inżynierskich, które likwidują te problemy.
Jednym z najbardziej kompleksowych rozwiązań w budownictwie domów drewnianych jest technologia prefabrykatów MiTek. Pozwala ona na wyjątkowo ekonomiczne i szybkie utworzenie szkieletu, wiązarów dachowych oraz stropu budynku.
MiTek jako firma nie produkuje wiązarów dachowych, a jedynie zajmuje się dystrybucją technologii. Kompleksowy system opiera się na trzech podstawowych elementach – maszynach, łącznikach oraz oprogramowaniu. Wdrażanie tej technologii wymaga spełnienia kilku określonych działań.
Na początek konieczne jest przeprowadzenie dokładnych obliczeń projektowych, uwzględniających wszystkie elementy konstrukcji. W tym celu stosuje się specjalistyczne oprogramowanie inżynierskie MiTek. Odpowiada ono za dobór łączników, a także sterowanie maszynami. Program służy do utworzenia projektu oraz dokumentacji technicznej. Opracowany został z myślą o producentach wiązarów dachowych i innych konstrukcji drewnianych, a nie pracownikach biur projektowych, co jest to podyktowane względami praktycznymi.
Oprogramowanie bierze pod uwagę przede wszystkim ostateczny koszt powstałej konstrukcji. Gotowy budynek nie może być zatem przewymiarowany, a przez to zbyt drogi w realizacji. Na etapie projektowania znaczenie mają także inne kwestie istotne dla producenta. Dotyczy to np. doboru przekrojów drewna dostępnych na magazynie, szybkich wycen czy podziału większych elementów do transportu.
Kolejny etap polega na utworzeniu elementów prefabrykowanych MiTek. Elementy konstrukcji muszą zostać najpierw wycięte z drewna. Sterowane numerycznie piły poprzeczne pozwalają na precyzyjne wycięcie elementów konstrukcji, które następnie poddawane są impregnacji.
Na kolejnym etapie przeprowadza się ich montaż. Łączenie elementów z drewna odbywa się za pomocą odpowiedniego sprzętu – MiTek dostarcza producentom piły jednotarczowe i wielotarczowe, a także różnego typu prasy hydrauliczne.
Do najpopularniejszych maszyn oferowanych przez firmę należą C-prasy. W przypadku tych stanowisk, głowica płytek wciskających ma kształt litery C. Szablon wiązara jest w stanie utworzyć zestaw stolików z blatem ruchomym oraz stałym magnesem u podstawy. Rozwiązanie to pozwala na zamocowanie ułożonego kształtu w taki sposób, a nie ulegał on rozsunięciu przy zdejmowaniu wiązara.
Jeszcze innym typem maszyny są prasy stołowe. W tym przypadku szablon układany jest na dużych stołach, a za wciskanie płytek odpowiada przesuwający się most. System MiTek ogranicza proces instalacji do podstawowego zamontowania konstrukcji, a następnie połączenia jej specjalnymi płytkami.
Do łączenia elementów więźby dachowej wykorzystuje się płytki kolczaste, przez co konstrukcje stropowe często nazywane są kratownicami. Dają one możliwość utworzenia wyjątkowo efektownego projektu aranżacyjnego dachu praktycznie każdego budynku.
Czym są płytki kolczaste MiTek?
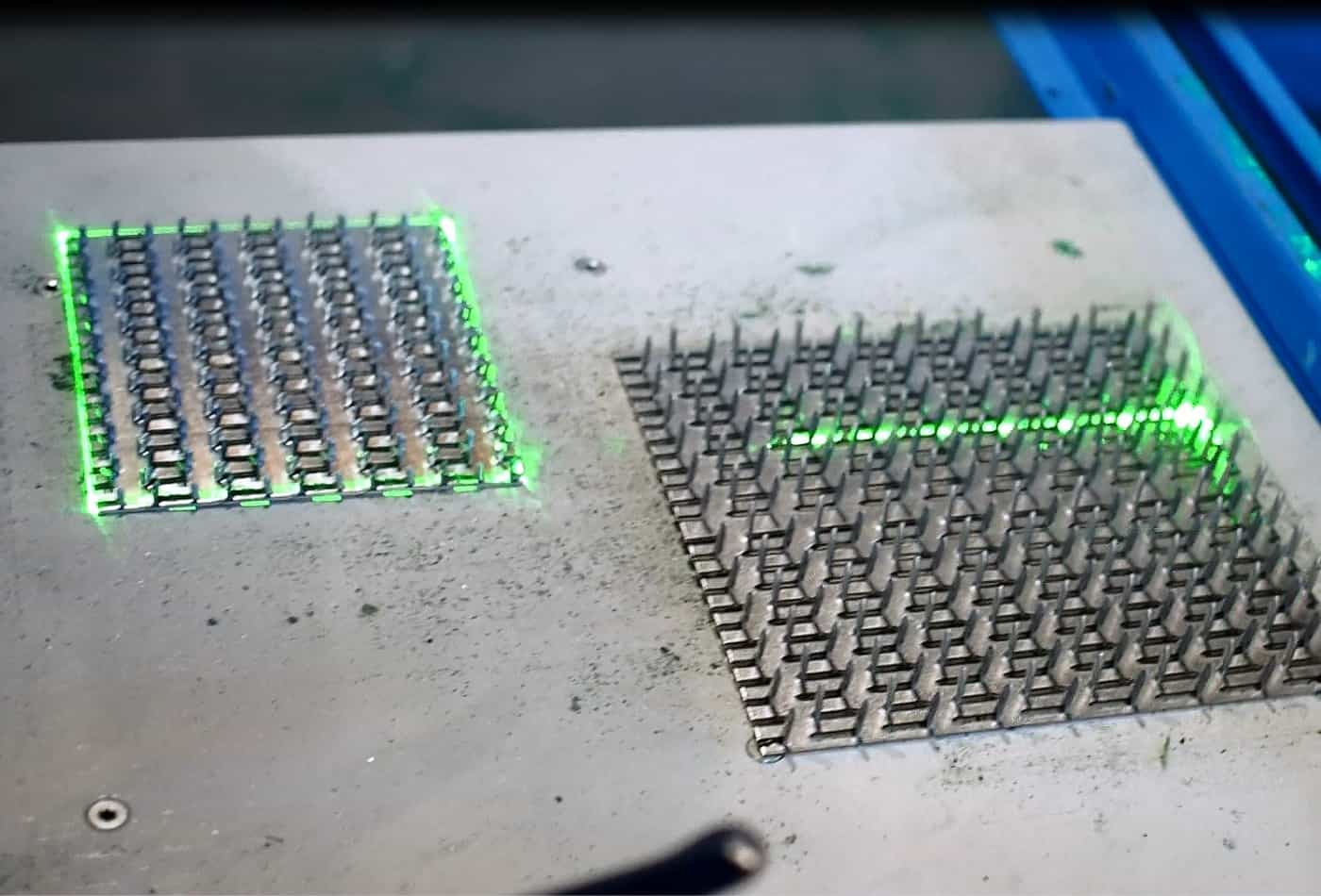
Płytki kolczaste MiTek
Płytka kolczasta znana jest również jako kolczatkowa, wielokolcowa i gwoździowa. To niezwykle istotny element łączenia konstrukcji drewnianych, nie tylko tych w systemie MiTek. Płytka kolczasta MiTek ma formę płyty ze stalowej blachy nierdzewnej lub ocynkowanej, posiadającej wytłoczenia w postaci kolców. Wtłacza się je bezpośrednio w elementy drewniane zetknięte ze sobą. W tym celu stosuje się specjalne prasy o wielotonowym nacisku, dzięki czemu powstaje trwałe i bardzo mocne połączenie.
Płytki kolczaste zostały wynalezione jeszcze w latach 50-tych, a z czasem coraz mocniej udoskonalano tę metodę łączenia wiązarów. W latach 80-tych elementy te zaczęli projektować także polscy konstruktorzy. Obecnie znajdują zastosowanie na całym świecie. W wielu ośrodkach badawczych prowadzone są testy wytrzymałości płytek kolczastych. Doświadczenia te mają na celu określenia ich przewidywalnej nośności, jakości i trwałości. Czynniki te w dużym stopniu decydują o obniżeniu kosztów postawienia drewnianej konstrukcji prefabrykowanej, nierzadko o nawet kilkadziesiąt procent.
Płytki kolczaste pozwalają na łączenie kilku elementów drewnianych o takiej samej grubości oraz w jednej płaszczyźnie. Mogą z powodzeniem zastąpić różne materiały spajające, takiej jak kleje i gwoździe. Rozwiązanie MiTek eliminuje ryzyko wystąpienia zjawiska koncentracji naprężeń. Łączniki posiadają wytłoczone kolce, które są równomiernie rozłożone i zaokrąglone.
Płytki kolczaste mogą występować w różnych wariantach kolorystycznych. Z powodzeniem sprawdzają się w wielu indywidualnych zastosowaniach. Płytki kolczaste MiTek wykorzystuje się w formie łączników nie tylko dla więźb dachowych domów, ale również zadaszeń obiektów handlowych, rolniczych, przemysłowych czy sportowych.
Służą do usztywniania narożników ścian szkieletowych oraz pokrywania już istniejących dachów płaskich. Łączone za pośrednictwem płytek kolczastych elementy drewniane zastępują konstrukcje stalowe i żelbetowe, a także te z drewna klejonego.
Do zalet tego rozwiązania należy możliwość dowolnego kształtowania połaci dachowej. Nie bez znaczenia pozostaje ograniczenie ciężaru całkowitego konstrukcji dachu, co przyspiesza i ułatwia montaż.
Technologia ta daje gwarancję zachowania prawidłowego kształtu konstrukcji oraz precyzji wykonywanych elementów. Uzyskane wymiary są powtarzalne i dokładne, co daje znakomity efekt końcowy. Płytki kolczaste dają możliwość dostarczenia na plac budowy kompletnych wiązarów, a także szybkiego zamontowania ich w całość. Umożliwiają wykonanie kształtów nietypowych, nierzadko na dużych rozpiętościach. Długotrwałe składowanie drewna na placu budowy nie jest dzięki temu konieczne.
Warunkiem uzyskania trwałości i bezpieczeństwa połączeń jest zastosowanie płytek kolczastych dobrej jakości. Powinny być wyprodukowane zgodnie z wszystkimi normami i wymogami.
Połączenie wykonane z płytek kolczastych zakłada wykorzystanie powierzchni płaskiej łączonych elementów. Zapewnia ona wytrzymałość i stabilność połączenia przy zachowaniu wysokiego poziomu odporności na bezpośrednie oddziaływanie dużych sił.
Płytki kolczaste dają możliwość wykonywania konstrukcji wiązarowych o rozpiętości sięgającej nawet do 30 metrów bez podpory. Połączenie to opiera się na równomiernym przejmowaniu obciążeń między jednym elementem a drugim. Niektóre konstrukcja pozwalają na uzyskanie połączenia o mocy nieodbiegającej od litego drewna.
Wiązary dachowe łączone płytkami kolczastymi charakteryzują się masą o wartości mniejszej, niż ma to miejsce w przypadku z tradycyjną więźbą dachową. Wykonanie wiązara z elementami łączonymi w ten sposób wymaga bardzo precyzyjnego wycięcia. Najczęściej wykorzystuje się w tym celu poprzeczne piły obrotowe, w których tarcze ustawione są pod odpowiednimi kątami. Większość współczesnych maszyn tego typu korzysta ze sterowania CNC.
Wiązary kratownicowe łączone płytkami kolczastymi to najczęściej spotykana prefabrykowana konstrukcja dachowa. Więźba tego typu najczęściej składa się z jednego pasa dolnego oraz dwóch pasów górnych, które odpowiadają standardowym krokwiom, skośnym krzyżulcom i słupkom pionowym.
Czas dostarczenia prefabrykatów na plac budowy to przeważnie około dwóch tygodni. Transportem i montażem wiązarów zwykle zajmuje się producent wiązarów MGDachy, jednak można to zrobić także we własnym zakresie.
Płytki kolczaste w technologii MiTek posiadają grubość 1-2 mm oraz wytłoczone kolce w wysokości 8-20 mm. Pod wpływem wprasowania pod naciskiem pras w stykające się elementy tarcicy, tworzone jest trwałe i mocne połączenie. Nie ma w tym przypadku potrzeby stosowania gwoździ, kleju czy śrub.
Taka konstrukcja umożliwia tworzenie dźwigarów o znacznej rozpiętości, a jednocześnie minimalizuje koszty przedsięwzięcia. Wynika to przede wszystkim z możliwości samodzielnego przeprowadzenia montażu lub skorzystania z usług producenta wiązarów MGDachy. Nie ma więc konieczności zlecenia usługi wykonani dachu zewnętrznej firmie.
Nie bez znaczenia pozostaje kwestia optymalizacji zużycia tarcicy przez oprogramowanie komputerowe. W zestawieniu z klasycznymi konstrukcjami, na samym materiale zaoszczędzić można 20-40 proc. budżetu.
Zakład prefabrykacji MGDachy często oferuje jeszcze niższe ceny. Spore oszczędności wiążą się także z zastosowaniem dolnego pasa w formie konstrukcji stopu. Rozwiązanie to sprawdza się zarówno w przypadku poddaszy nieużytkowych, jak i użytkowych. W ten sposób wyeliminować można drogi strop betonowy, a tym samym zaoszczędzić na zastosowaniu lżejszych fundamentów i ścian zewnętrznych.
Dzięki sporym rozpiętościom stropów prefabrykowanych można też wyeliminować ściany nośne wewnątrz budynku, co przekłada się na obniżenie kosztów inwestycji i zwiększenie możliwości aranżacji wnętrza.
Dodatkowe oszczędności wynikają ze zmniejszenia zakresu robót montażowych w obiekcie. W ten sposób da się przyspieszyć czas budowy. Ze względu na możliwość wykonywania dachu nawet w okresie zimowym, sezon budowlany można bez przeszkód wydłużyć.
Czym są belki prefabrykowane Posi Joist?
Do wzniesienia konstrukcji stropu drewnianego wykorzystać można prefabrykowane belki Posi Joist. W tym przypadku elementy dolnego i górnego pasa są łączone specjalnymi krzyżulcami wykonanymi z blach stalowych, znanymi jako Posi Strut. Belki stropowe Posi Joist są lekkie niczym drewno, a mimo to posiadają siłę stalowej sieci.
Konstrukcja pozostaje sztywna nawet przy stosunkowo niskiej wadze. Łączniki występują w wielu wariantach rozmiarowych.
Posi Joist mają różne przekroje, w zależności od poziomu obciążeń oraz rozpiętości. Do ich zalet należy nie tylko solidność i stabilność, ale również wysoki poziom estetyczny. Posi Joist sprawdzają się w przypadku konstrukcji dachów płaskich. Przy braku podpory rozpiętość może wynieść do 6 metrów, z założeniem użytkowego obciążenia na poziomie równym stropom betonowym, obciążeń od ścianek działowych oraz obciążeń od warstw. Szerokie rozpiętości elementów prefabrykowanych zapewniają sporą swobodę w kształtowaniu wnętrz obiektów ze stropem drewnianym.
W rezultacie różnorodność pod względem projektowania układów wewnętrznych może być bardzo duża. Posi Joist spotykane są zarówno w obiektach mieszkalnych, jak i przemysłowych. Rozwiązanie to charakteryzuje się o nawet połowę mniejszym ciężarem, niż stropy betonowe. Pozwala tym samym na zastosowanie cięższego stropu drewnianego, posiadającego warstwy tłumiące dźwięki, dociążające czy przeciwogniowe.
Technologia prefabrykacji Posi Joist zapewnia sporą oszczędność materiałową oraz finansową. Inwestor może znacząco obniżyć koszty surowców, a także zmniejszyć wydatki związane z robocizną. Uzyskana konstrukcja jest bardzo lekka, przez co można uniknąć stosowania wieńca. Przekrój fundamentów i ścian nośnych da się bez trudu zmniejszyć.
W zależności od indywidualnego projektu, zredukować lub całkowicie wyeliminować można podpory. W przypadku Posi Joist nie ma potrzeby stosowania dźwigów, co ogranicza koszty montażu. Z uwagi na niedużą wagę elementów prefabrykowanych, strop montowany jest bez udziału specjalistycznych maszyn. Nierzadko da się go przeprowadzić całkowicie we własnym zakresie.
Konstrukcja belek stropowych Posi Joist jest ażurowa, co przyspiesza i ułatwia prowadzenie instalacji wewnątrz budynku – np. elektrycznej, kanalizacyjnej czy wodnej. Takie rozwiązanie dodatkowo niweluje koszty. Na oszczędność wpływa też brak stempli i podpór tymczasowych w czasie montażu. Technologia prefabrykacji Posi Joist nie wymaga prowadzenia prac betonowych.
Nie trzeba stosować wylewek, które z powodzeniem zastępują warstwy kruszywa. Rozwiązanie to oszczędza przede wszystkim czas, którego potrzebuje beton do wyschnięcia i nabrania pożądanych właściwości konstrukcyjnych.
Do zalet stropu drewnianego prefabrykowanego Posi Joist należy prostota i szybkość jego montażu. Otwory i łącznie z murem wykonywane są za pomocą specjalnych okuć. Komplet prac można ukończyć bardzo szybko, dzięki czemu strop gotowy jest do użytku nawet w ciągu jednego dnia. Poprawne wykonanie i zastosowanie odpowiednich warstw wygłuszających nadaje belkom dobrą izolacyjność akustyczną i termiczną.
Posi Joist często spotykane są w budynkach energooszczędnych, ze względu na możliwość wyłożenia grubych warstw wełny mineralnej. Ażurowa konstrukcja umożliwia umieszczenie jej na etapie prasowania między krzyżulcami. W ten sposób eliminowane jest ryzyko wystąpienia mostków termicznych. Do dolnego pasa belki można natomiast bezpośrednio zamocować wybrany materiał sufitowy.
Technologia Posi Joist jest ponadto sposobem na usztywnienie podłogi oraz zredukowanie nachalnych skrzypień. Przekroje belek można łatwo dostosować do wymagań architektonicznych i wytrzymałościowych budynku jeszcze na etapie jego projektu.
FAQ
Jaką rozpiętość mogą mieć wiązary prefabrykowane?
Płytki kolczaste dają możliwość wykonywania konstrukcji wiązarowych o rozpiętości sięgającej nawet do 30 metrów bez podpory.
Jakie są zalety technologii MiTek?
Jednym z najbardziej kompleksowych rozwiązań w budownictwie domów drewnianych jest technologia prefabrykatów MiTek. Pozwala ona na wyjątkowo ekonomiczne i szybkie utworzenie szkieletu, wiązarów dachowych oraz stropu budynku.
Co to są płytki kolczaste?
Płytka kolczasta MiTek ma formę płyty ze stalowej blachy nierdzewnej lub ocynkowanej, posiadającej wytłoczenia w postaci kolców. Wtłacza się je bezpośrednio w elementy drewniane zetknięte ze sobą. W tym celu stosuje się prasy o wielotonowym nacisku, dzięki czemu powstaje trwałe i bardzo mocne połączenie.